Flash butt welding is a widely used process in the metalworking industry, and it plays a crucial role in joining metal components. When using a flash butt welding machine, it is essential to assess the weldability of the metals involved to ensure a successful and durable weld. In this article, we will explore how to evaluate the weldability of metals when using a flash butt welding machine.
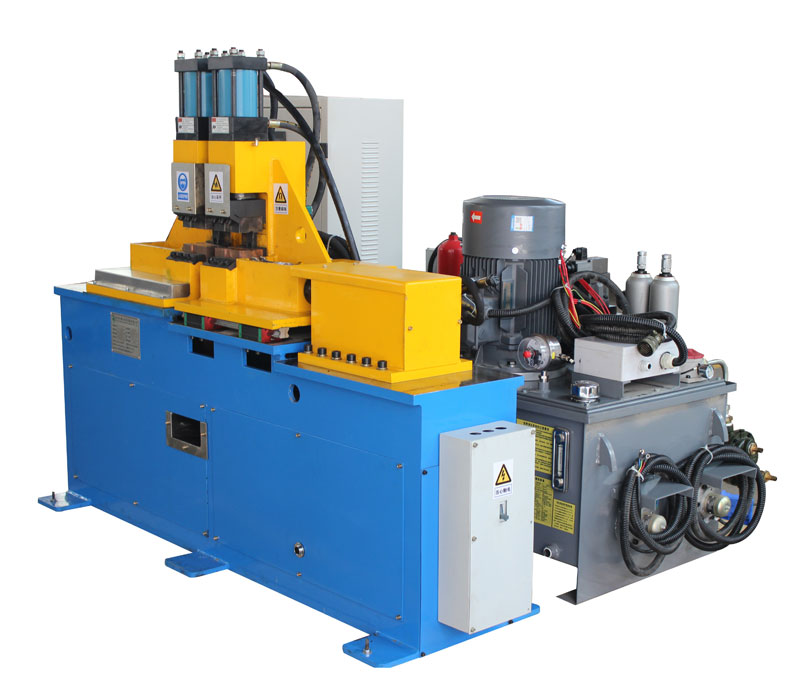
Understanding Weldability:
Weldability is the ability of a material to be successfully welded, maintaining the desired mechanical properties and structural integrity. It depends on several factors, including the material’s chemical composition, mechanical properties, and the welding process itself. In flash butt welding, the focus is primarily on assessing the material’s suitability for the specific process.
Assessing Weldability:
- Material Compatibility: The first step in determining weldability is to ensure that the metals to be joined are compatible. Metals with similar chemical compositions and properties are more likely to be successfully welded. It’s crucial to refer to material specifications and guidelines to confirm compatibility.
- Cleanliness: Proper surface preparation is essential for successful flash butt welding. The metals should be free from contaminants, such as rust, oil, and dirt, which can negatively impact the weld quality. Thorough cleaning and surface treatment are necessary.
- Material Thickness: The thickness of the materials being welded can impact weldability. Flash butt welding is particularly suited for thicker materials, but it can be used for a range of thicknesses. It’s important to ensure that the machine and parameters are adjusted accordingly.
- Heat Conductivity: Metals with significantly different heat conductivities can pose challenges during flash butt welding. Materials with similar thermal conductivities are easier to weld, as they heat and cool at a more consistent rate.
- Machine Settings: Flash butt welding machines have various settings that can be adjusted to accommodate different materials. These settings include welding current, upset force, and welding time. Proper adjustment is critical for achieving a strong and reliable weld.
- Testing and Inspection: Prior to full-scale welding, it’s advisable to conduct test welds to evaluate the quality of the weld and make any necessary adjustments. Non-destructive testing methods, such as radiography and ultrasonic testing, can be used to inspect the welds for defects.
In summary, flash butt welding is a versatile and efficient process for joining metals, but successful welds depend on the careful assessment of weldability factors. By considering material compatibility, cleanliness, thickness, heat conductivity, machine settings, and conducting thorough testing and inspection, you can determine the weldability of metals and ensure the quality of your welds. This diligence will lead to reliable, durable, and safe metal joints for a wide range of applications in the metalworking industry.