In the realm of manufacturing and fabrication, the design of a resistance spot welding fixture and welding device is a critical process that directly impacts the quality and efficiency of welding operations. These fixtures and devices are essential for ensuring accurate, repeatable, and secure welds in a variety of applications. In this article, we will explore the key considerations and steps involved in designing these crucial components.
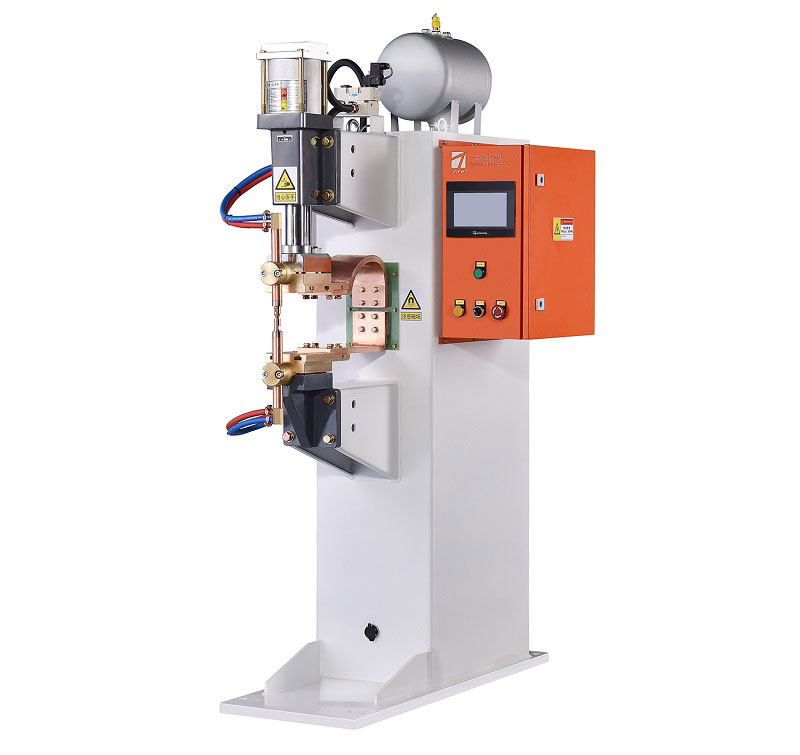
Understanding the Basics
Before delving into the design process, it’s essential to have a solid grasp of what resistance spot welding is. This welding technique involves the joining of two metal surfaces by applying pressure and passing an electric current through them. The heat generated from the electrical resistance melts the metal, forming a strong bond upon cooling. To achieve consistent and reliable welds, the right fixture and welding device must be in place.
Designing the Fixture
- Material Selection: The first step in designing a welding fixture is choosing the right materials. The fixture needs to withstand the heat generated during welding and maintain its structural integrity. Copper and its alloys are commonly used for their excellent electrical conductivity and heat resistance.
- Geometry and Dimensions: The fixture’s shape and dimensions should align with the specific welding requirements. It should provide adequate support to the workpieces, ensuring they maintain precise alignment during welding. The fixture’s geometry should also allow for easy loading and unloading of workpieces.
- Electrode Configuration: The electrodes are critical components that deliver the electrical current to the workpieces. They should be designed to match the shape of the weld and ensure uniform pressure distribution. Proper electrode cooling is also essential to prevent overheating.
- Clamping Mechanism: The fixture must securely hold the workpieces in place during welding. The clamping mechanism should be adjustable to accommodate different workpiece sizes and shapes. It should apply consistent pressure to ensure a strong weld.
Designing the Welding Device
- Power Supply: The welding device’s power supply should provide the necessary electrical current and voltage levels for the specific welding application. It should be adjustable to accommodate different materials and thicknesses.
- Control System: A precise control system is crucial for managing the welding process. It should allow for adjustments in welding parameters such as current, time, and pressure. Some modern welding devices are equipped with automated control systems that enhance repeatability.
- Cooling System: To prevent overheating and prolong the life of the welding electrodes and other components, a cooling system is essential. This can include water cooling for electrodes and transformers.
- Safety Features: Safety should be a top priority in the design of the welding device. It should include features like emergency stop buttons, overcurrent protection, and fault detection systems.
Designing a resistance spot welding fixture and welding device is a meticulous process that requires a deep understanding of welding principles and the specific requirements of the intended application. When executed correctly, these components play a pivotal role in achieving high-quality welds that meet industry standards. Manufacturers must invest time and effort into their design to ensure the reliability and efficiency of their welding operations.