Controlling the preload time is a critical aspect of the welding process in nut welding machines. This article explains the significance of preload time and provides insights into how it can be effectively managed to achieve consistent and reliable welds.
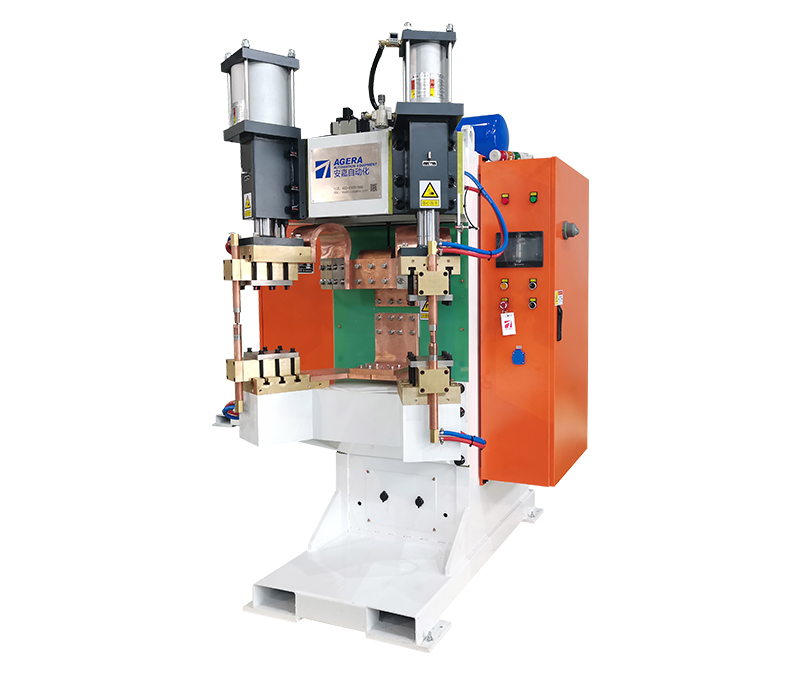
- Understanding Preload Time: Preload time refers to the duration during which the electrodes apply pressure to the nut and workpiece before the welding current is activated. This preliminary pressure, known as preload, ensures proper contact between the components and minimizes air gaps, leading to a more stable and secure weld joint.
- Importance of Preload Time: Properly controlling the preload time is essential for achieving optimal weld quality. An adequate preload time allows the surfaces to make intimate contact, reducing the risk of irregular welds and potential voids. Additionally, it promotes better heat conduction, resulting in a more uniform and efficient welding process.
- Factors Influencing Preload Time: Several factors influence the ideal preload time in nut welding machines, including the nut material, workpiece thickness, welding current, and electrode force. Understanding these variables and their impact on the welding process is crucial for determining the appropriate preload time for specific applications.
- Monitoring and Adjusting Preload Time: To achieve consistent welds, it is essential to monitor and control the preload time accurately. Advanced nut welding machines may be equipped with sensors and automated systems to precisely measure and adjust the preload time based on real-time data during the welding process.
- Manual Preload Time Control: In instances where automation is not available, operators can manually control the preload time. This involves using visual and tactile feedback to ensure that the electrodes are applying adequate pressure for the required duration before initiating the welding process.
- Optimizing Preload Time for Different Applications: Different nut welding applications may require variations in preload time to accommodate specific materials and joint configurations. Conducting tests and trials on sample welds can help identify the ideal preload time for each unique application.
- Maintaining Consistency: Consistency is key in achieving high-quality welds. Operators should strive to maintain consistent preload times throughout the welding operation, avoiding abrupt changes that could impact weld integrity.
Controlling the preload time in nut welding machines is a fundamental aspect of ensuring weld quality and joint strength. By understanding the significance of preload time, considering influencing factors, and implementing precise control measures, manufacturers can enhance the efficiency and reliability of their welding processes. Properly managed preload time contributes to producing robust and durable welds, making nut welding machines an indispensable tool in various industries.