Resistance spot welding is a widely used technique in various industries, such as automotive and aerospace, for joining metal components. One crucial aspect of this process is controlling the heating element, which plays a significant role in achieving strong and consistent welds. In this article, we will explore different heating control methods for resistance spot welding machines.
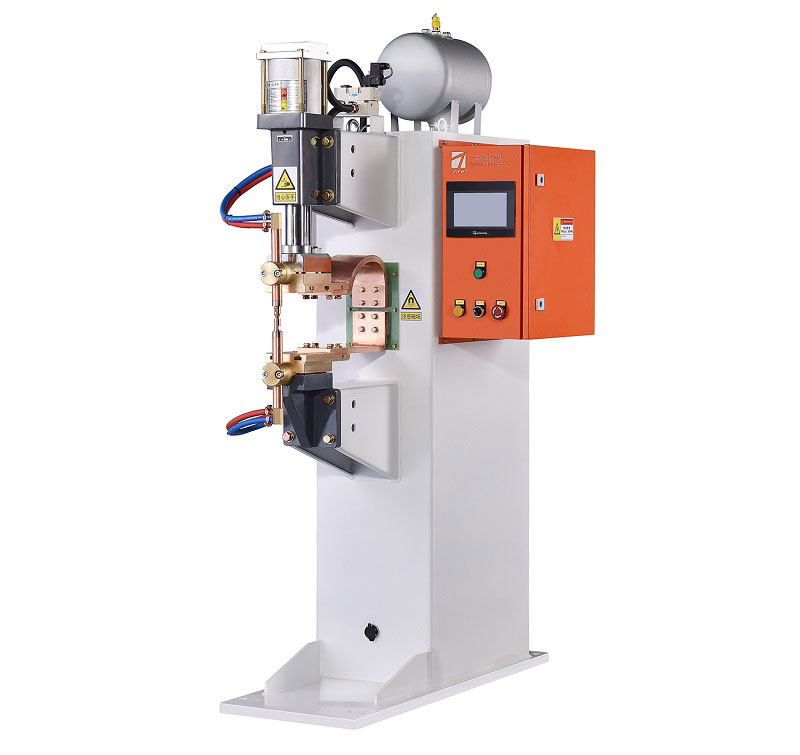
- Time-Based Control: This is one of the simplest methods where the heating element is energized for a predetermined period. The operator sets the welding time, and the machine applies current to the electrodes for that duration. While this method is straightforward, it may not be ideal for all materials and thicknesses, as it doesn’t consider variations in resistance or other factors that can affect the weld quality.
- Constant Current Control: In this method, the welding machine maintains a constant current throughout the welding process. This approach is effective for consistent welds, especially when dealing with materials with varying resistances. However, it requires precise control to prevent overheating or underheating, which can weaken the weld.
- Adaptive Control: Adaptive control systems use sensors to monitor the resistance during the welding process. These sensors provide real-time feedback to the machine, allowing it to adjust the current and timing as needed to achieve the desired weld quality. This method is highly effective for maintaining weld consistency and quality.
- Pulse Control: Pulse control is a versatile method that involves alternating between high and low current levels in a controlled manner. This can help reduce heat buildup, minimize distortion, and control the weld’s overall quality. Pulse control is particularly useful for thin materials and when joining dissimilar metals.
- Closed-Loop Control: Closed-loop control systems combine various sensors, such as temperature and displacement sensors, to continuously monitor and adjust the welding parameters. These systems offer precise control and are often used in automated welding processes to ensure consistent results.
- Induction Heating: In some specialized applications, resistance spot welding machines incorporate induction heating to preheat the materials before the actual welding process. This method can improve the weld’s quality by reducing thermal stress and enhancing material flow during welding.
- Simulation and Modeling: Advanced welding systems may utilize computer simulations and modeling to predict and optimize the heating process. These simulations consider various factors, such as material properties, electrode geometry, and current flow, to optimize the welding parameters for the best results.
In conclusion, the choice of heating control method for a resistance spot welding machine depends on factors such as the materials being joined, the desired weld quality, and the level of automation required. By understanding and selecting the appropriate heating control method, manufacturers can ensure consistent and high-quality welds in their production processes.