Surface burns, also known as burn marks or surface damage, can occur during the nut spot welding process. These burn marks are defects that affect the appearance and integrity of the weld joint. This article aims to explore the formation of surface burns in nut spot welding, discussing the causes and factors that contribute to their occurrence.
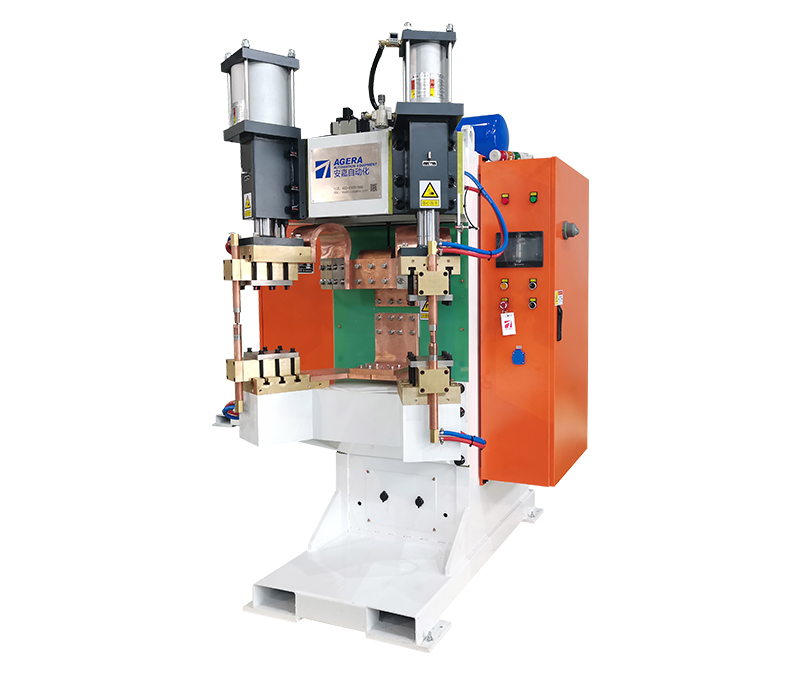
- High Heat Input: One of the primary causes of surface burns in nut spot welding is excessive heat input. When the welding parameters, such as current or time, are set too high, an excessive amount of heat is generated. This excess heat can result in the burning or scorching of the surface layers of the nut or workpiece, leading to the formation of burn marks.
- Inadequate Cooling: Insufficient cooling can also contribute to the formation of surface burns. During the welding process, proper cooling is necessary to dissipate the heat generated and prevent excessive heating of the surrounding areas. Inadequate cooling, such as insufficient water flow in the cooling system or improper electrode contact, can result in localized overheating and subsequent surface burns.
- Improper Electrode Selection: The selection of the electrode plays a crucial role in preventing surface burns. If the electrode material is not suitable for the specific nut and workpiece combination, it may have a poor heat transfer capability or inadequate cooling properties. This can lead to localized overheating and the formation of burn marks on the surface.
- Contamination: Contamination on the surface of the nut or workpiece can contribute to the formation of surface burns. Oil, grease, or other foreign substances present on the surface can ignite or create excessive smoke when exposed to the high temperatures during welding. This can result in burn marks on the weld surface.
- Inconsistent Pressure: Inconsistent pressure exerted during the welding process can also contribute to the formation of surface burns. If the pressure is too high or unevenly distributed, it can cause localized overheating and scorching of the surface layers. Proper pressure control and uniform force application are essential to prevent surface burn defects.
Prevention and Mitigation: To minimize the occurrence of surface burns in nut spot welding, several measures can be taken:
- Optimize welding parameters, such as current, time, and pressure, to ensure they are within the recommended range for the specific nut and workpiece combination.
- Ensure proper cooling by maintaining an adequate water flow rate and optimizing electrode cooling mechanisms.
- Select suitable electrodes with good heat transfer properties and consider their compatibility with the nut and workpiece materials.
- Clean and prepare the surfaces of the nut and workpiece to remove any contaminants or foreign substances before welding.
- Implement consistent and uniform pressure application during the welding process.
Surface burns in nut spot welding are defects that can negatively impact the appearance and structural integrity of the weld joint. Understanding the causes and factors contributing to their formation allows for proactive measures to prevent or mitigate their occurrence. By optimizing welding parameters, ensuring proper cooling, selecting suitable electrodes, maintaining surface cleanliness, and applying consistent pressure, welders can minimize the risk of surface burns and achieve high-quality nut spot welds.