Resistance spot welding is a widely used process in the manufacturing industry for joining metal components. However, one common issue that operators often encounter is electrode wear. Electrode wear can significantly impact the quality of welds and the efficiency of the welding process. In this article, we will explore the factors that contribute to electrode wear in resistance spot welding machines.
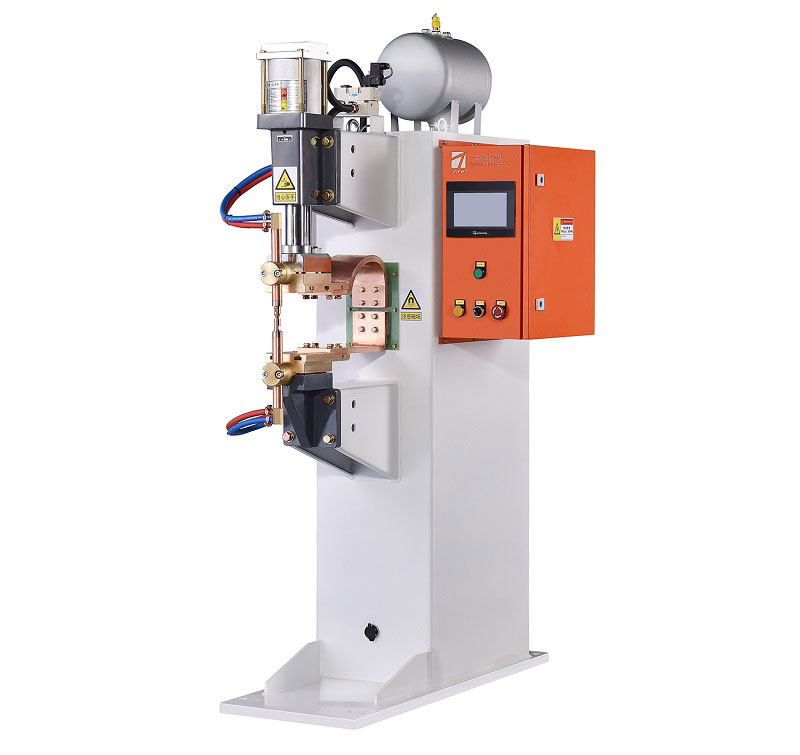
- Material Hardness: The hardness of the electrode material plays a crucial role in its wear resistance. Softer materials tend to wear out more quickly than harder ones. Manufacturers often use copper alloys for electrodes due to their good electrical conductivity and moderate hardness. However, even within these materials, variations in hardness can affect wear rates.
- Welding Current: The welding current used during the process directly influences electrode wear. Higher welding currents generate more heat at the electrode tips, causing them to wear out faster. Finding the right balance between current and electrode life is essential for optimizing welding operations.
- Welding Time: Prolonged welding times can accelerate electrode wear. Longer welding durations lead to extended exposure to heat and pressure, which can erode the electrode material. Adequate cooling and electrode rotation strategies can help mitigate wear in these situations.
- Electrode Force: The force applied to the electrodes affects both the quality of the weld and electrode wear. Excessive force can cause electrode deformation and increase wear. On the other hand, insufficient force can lead to poor weld quality. Maintaining the correct electrode force is critical in minimizing wear.
- Electrode Contamination: Contaminants on the workpiece, such as rust, paint, or oil, can accelerate electrode wear. These substances can adhere to the electrode surface and degrade its performance. Proper workpiece preparation and regular electrode cleaning are essential preventive measures.
- Electrode Design: The design of the electrodes, including their shape and size, can impact wear. Well-designed electrodes distribute current evenly, reducing localized heating and wear. Electrode materials can also be treated or coated to enhance their wear resistance.
- Cooling Systems: Inadequate cooling can lead to excessive electrode temperatures, causing accelerated wear. Efficient cooling systems, such as water or air-cooling, are crucial for maintaining the electrode’s temperature within an acceptable range.
- Workpiece Material: The material being welded also influences electrode wear. Harder and more abrasive materials will generally cause faster electrode wear compared to softer materials.
- Operator Skill and Training: The expertise of the operator plays a vital role in electrode wear. Proper training and skill development can help operators make informed decisions regarding welding parameters and techniques to minimize wear.
In conclusion, electrode wear in resistance spot welding machines is influenced by multiple factors. Understanding these factors and their interactions is crucial for optimizing welding processes, reducing downtime, and achieving high-quality welds. By carefully managing material selection, welding parameters, and maintenance practices, manufacturers can extend the life of electrodes and improve the overall efficiency of their welding operations.