In the realm of manufacturing, spot welding is a widely utilized technique, particularly in the automotive and construction industries. It involves joining two pieces of metal by applying heat and pressure at a specific point. To achieve a successful spot weld, it’s crucial to control various parameters, one of which is the distribution of electric current, especially in nut spot welding machines. This article delves into the factors that influence the distribution of electric current in such machines.
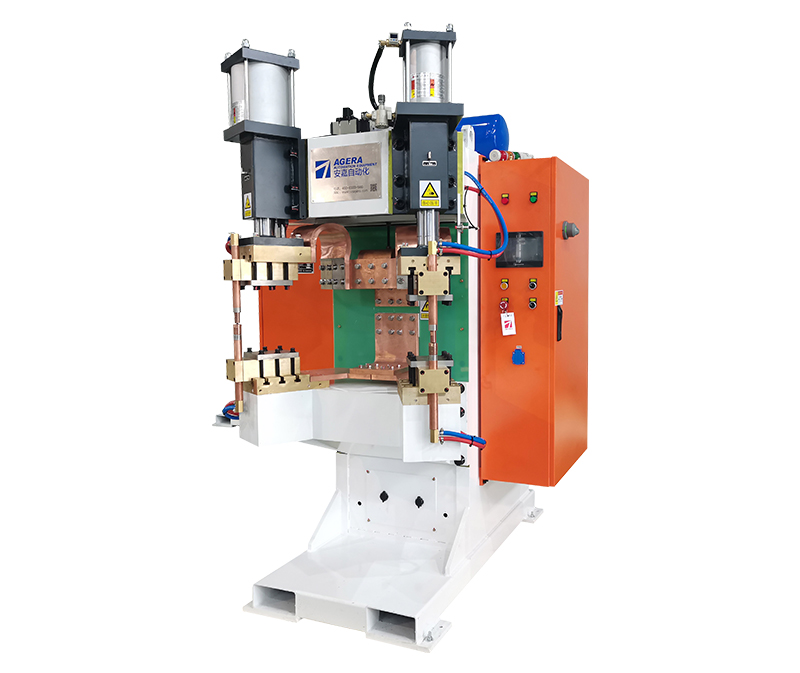
Factors Affecting Current Distribution:
- Material Conductivity: The electrical conductivity of the materials being welded greatly influences current distribution. Materials with higher conductivity, such as copper or aluminum, allow for more even current distribution. In contrast, materials with lower conductivity, like certain types of steel, may require adjustments to the welding process to ensure uniformity.
- Electrode Design: The design and material of the welding electrodes play a significant role in current distribution. Electrodes that are not properly aligned or have irregular surfaces can result in uneven contact and, consequently, uneven current distribution.
- Pressure and Contact Area: Proper pressure and a sufficient contact area between the electrodes and the workpieces are essential. Inadequate pressure or a small contact area can lead to poor current distribution as the electrical resistance increases at the contact point.
- Electrode Force Control: The force with which the electrodes apply pressure affects current distribution. An improperly set force can lead to an imbalance in the distribution of current, resulting in inconsistent welds.
- Welding Machine Settings: Parameters such as welding current, welding time, and electrode force are set in the welding machine. Accurate calibration of these settings is crucial to ensure consistent and reliable current distribution during the welding process.
- Electrode Wear: As electrodes wear over time, their condition can deteriorate, affecting their ability to conduct current evenly. Regular maintenance and replacement of worn electrodes are necessary to maintain uniform current distribution.
- Workpiece Thickness and Geometry: The thickness and geometry of the workpieces being welded can also impact current distribution. Variations in these factors may require adjustments in the welding process to maintain uniformity.
Achieving consistent and reliable current distribution in nut spot welding machines is critical for producing high-quality welds. Manufacturers must consider a range of factors, including material conductivity, electrode design, pressure, electrode force control, machine settings, electrode wear, and workpiece characteristics. By addressing these factors, manufacturers can enhance the efficiency and quality of their spot welding processes, ensuring that each weld is strong and reliable.