Flash butt welding is a critical process in various industries, such as automotive, construction, and manufacturing. The external defects in the welding process can have a significant impact on the quality and integrity of the welds. In this article, we will explore the various external defect morphologies encountered in flash butt welding and their implications.
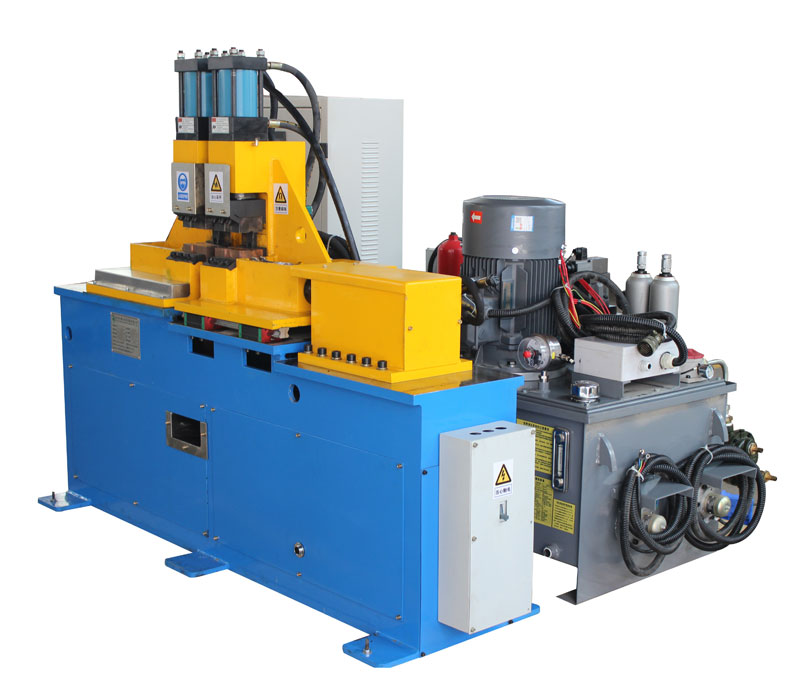
- Surface Contamination: Surface contamination is one of the most common external defects in flash butt welding. It can be caused by the presence of rust, oil, grease, or other foreign materials on the surfaces of the workpieces. When these contaminants are not properly removed before the welding process, they can lead to poor fusion and weak welds. In addition, surface contamination can also result in a lack of uniform heating, affecting the overall quality of the weld joint.
- Misalignment: Misalignment of workpieces is another issue that can lead to external defects. When the workpieces are not properly aligned, it can result in uneven heating and pressure distribution during the welding process. This can lead to defects such as weld flash, excessive deformation, and even weld cracking. Proper fixturing and alignment are essential to avoid these issues.
- Inadequate Pressure: Insufficient pressure during the flash butt welding process can result in poor-quality welds. When the pressure is not applied uniformly, it can lead to defects like undercuts and lack of fusion. Adequate pressure is crucial to ensure proper metallurgical bonding between the workpieces.
- Electrode Contamination: Contaminated or worn electrodes can also contribute to external defects. Electrodes that are not in good condition can lead to variations in heat distribution, which can cause defects like craters and excessive burning. Regular maintenance and replacement of electrodes are necessary to maintain welding quality.
- Inconsistent Flash: In flash butt welding, the duration and intensity of the flash are critical factors that can affect the weld quality. Inconsistent flashing can result in defects such as overheating or insufficient heating. Proper control of the flash parameters is essential to achieve uniform and high-quality welds.
- Material Incompatibility: Using incompatible materials for flash butt welding can result in external defects and weld joint failure. Different materials have varying melting points and thermal conductivities, which can lead to issues like incomplete fusion, cracks, and brittle welds. It’s essential to select materials that are compatible with each other for successful welding.
In conclusion, understanding the external defect morphologies in flash butt welding is crucial for ensuring the quality and reliability of weld joints. Proper preparation, alignment, pressure control, electrode maintenance, and control of flashing parameters are essential for minimizing external defects and producing high-quality welds. By addressing these issues, manufacturers can improve the overall performance and durability of their flash butt welding processes.