Resistance spot welding is a vital technique in manufacturing and metalwork industries. This process joins metal pieces together by applying pressure and heat, creating a strong and reliable bond. To achieve the best results and ensure safety, it’s crucial to master the operation of resistance spot welding machines. In this article, we will delve into essential tips and techniques for effectively using these machines.
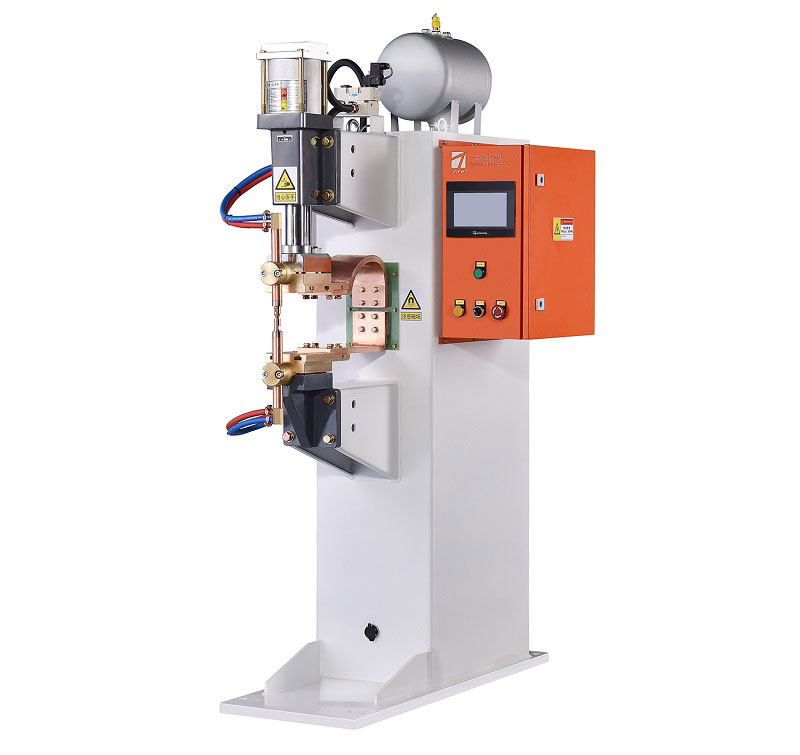
- Safety First Before we dive into the operation of resistance spot welding machines, it’s paramount to prioritize safety. Always wear appropriate personal protective equipment (PPE), including gloves, safety glasses, and flame-resistant clothing. Ensure that your work area is well-ventilated to disperse fumes generated during welding.
- Machine Setup Start by inspecting the welding machine to ensure it’s in proper working condition. Check the electrodes for wear and damage, and replace them if needed. Adjust the electrode force and welding current according to the material thickness and type you are welding. Refer to the machine’s manual for specific settings.
- Material Preparation Prepare the materials to be welded by cleaning and degreasing them. Any contaminants on the surface can affect the quality of the weld. Ensure that the metal pieces are correctly aligned and held firmly in place using clamps or fixtures.
- Electrode Placement Proper electrode placement is crucial for a successful weld. Position the electrodes perpendicular to the materials being joined and ensure they make good contact. Misalignment or improper electrode contact can result in weak welds.
- Welding Technique The welding process involves pressing the electrodes against the materials and passing a high current through them for a specific duration. Maintain consistent pressure and control the welding time to create a uniform and strong weld nugget. The appropriate welding time and current settings will depend on the material thickness and type.
- Cooling After welding, allow the welded area to cool naturally or use a cooling method recommended for the material. Rapid cooling can lead to cracking or other defects in the weld.
- Inspect and Test Always inspect the weld for quality. Look for any signs of defects, such as cracks, voids, or irregularities. If necessary, perform non-destructive testing methods, such as dye penetrant testing or X-ray examination, to ensure the integrity of the weld.
- Maintenance Regularly maintain your resistance spot welding machine to keep it in optimal condition. Clean the electrodes, check for wear, and lubricate moving parts as recommended by the manufacturer. A well-maintained machine ensures consistent and high-quality welds.
In conclusion, mastering the operation of resistance spot welding machines requires attention to detail and a commitment to safety. By following these tips and techniques, you can create strong and reliable welds while ensuring a safe working environment. Remember to consult the machine’s manual and seek training if you are new to spot welding to maximize your proficiency in this essential manufacturing process.