Capacitor Discharge (CD) spot welding machines are widely used in various industries for their ability to deliver precise and efficient spot welds. The welding process in these machines involves several distinct phases of welding time, each contributing to the overall quality and integrity of the weld joint. This article explores the different phases of welding time in CD spot welding machines and their significance in achieving optimal weld results.
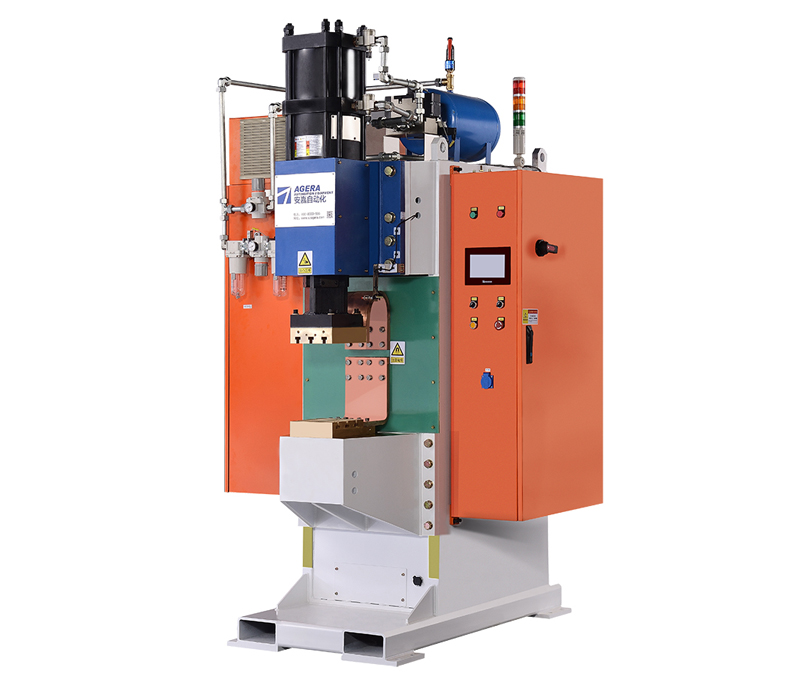
Phases of Welding Time:
- Contact Phase: In the contact phase, the electrodes make physical contact with the workpieces to be welded. This initial contact establishes a conductive path between the electrodes and the workpieces. The contact phase is essential for ensuring a consistent and stable electrical connection.
- Pre-Weld Phase: Following the contact phase, the pre-weld phase begins. During this phase, a predetermined amount of energy is charged into the welding capacitor. This energy buildup is critical to achieving a sufficient energy level for proper weld nugget formation.
- Welding Phase: The welding phase is the moment when the charged energy in the capacitor is discharged through the electrodes and into the workpieces. The intense energy release creates a localized fusion between the materials, forming the weld nugget. The duration of the welding phase directly affects the weld penetration and joint strength.
- Post-Weld Phase: After the welding phase, there is a post-weld phase during which the electrodes remain in contact with the workpieces to allow the weld nugget to solidify and cool. This phase contributes to the development of a strong and durable weld joint.
- Cooling Phase: Once the post-weld phase is complete, the cooling phase begins. During this phase, the electrodes are fully retracted, and any residual heat in the weld zone dissipates. Effective cooling helps prevent overheating and distortion of the welded components.
The welding time in Capacitor Discharge spot welding machines is divided into several distinct phases, each playing a crucial role in achieving high-quality welds. The contact phase establishes a stable connection, the pre-weld phase builds up energy, the welding phase creates the weld nugget, the post-weld phase allows for solidification, and the cooling phase prevents overheating. Manufacturers and operators must carefully consider and optimize each phase’s duration to ensure consistent weld quality, joint strength, and overall process efficiency. By understanding and controlling these phases, CD spot welding machines can produce reliable and robust welds across various applications.