In energy storage spot welding machines, accurately determining the thickness of workpieces is crucial for achieving optimal weld quality and ensuring the welding process is properly configured. This article discusses various methods for assessing workpiece thickness in energy storage spot welding machines, enabling operators to make informed decisions regarding welding parameters and electrode selection.
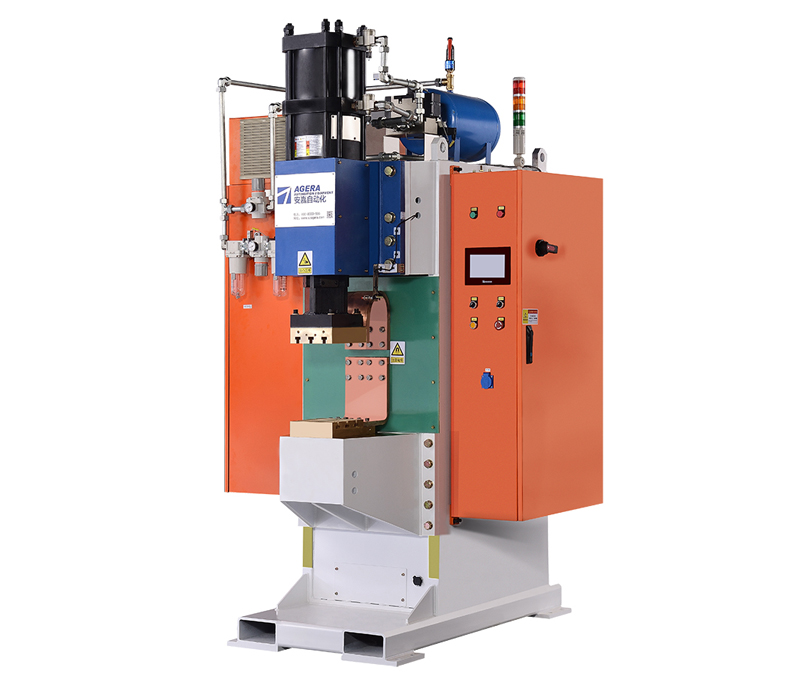
- Calibrated Thickness Gauges: One of the simplest and most reliable methods to determine workpiece thickness is by using calibrated thickness gauges. These gauges are precision instruments that provide accurate measurements of the material thickness. Operators can place the gauge directly on the workpiece to obtain an immediate reading, allowing them to select the appropriate welding parameters based on the workpiece thickness.
- Ultrasonic Thickness Testing: Ultrasonic thickness testing is a non-destructive testing technique that uses ultrasonic waves to measure the thickness of materials. It involves sending ultrasonic pulses into the workpiece and analyzing the reflected waves to determine the material thickness. Ultrasonic thickness testers are widely available and provide accurate results for various materials, including metals.
- Laser-based Measurement Systems: Advanced laser-based measurement systems utilize laser sensors to measure the distance from the sensor to the workpiece surface accurately. By scanning the surface, these systems can provide precise thickness measurements. Laser-based measurement systems are particularly useful for complex workpiece geometries or situations where direct contact measurement is challenging.
- Comparative Analysis: For certain applications, operators can rely on a comparative analysis approach. By comparing the workpiece thickness with a reference sample or known standard, operators can estimate the thickness of the workpiece. This method is suitable when a high level of accuracy is not required, and the focus is on relative thickness rather than absolute values.
- Manufacturer Specifications and Documentation: Workpiece thickness information may be provided in the manufacturer’s specifications or documentation for the specific welding machine. Operators should consult the machine’s user manual or contact the manufacturer for guidance on determining workpiece thickness and recommended welding parameters.
Accurately determining workpiece thickness is vital in energy storage spot welding machines to ensure proper configuration of welding parameters and electrode selection. By utilizing calibrated thickness gauges, ultrasonic thickness testing, laser-based measurement systems, comparative analysis, and referring to manufacturer specifications, operators can confidently assess workpiece thickness and make informed decisions for achieving high-quality welds. Understanding the workpiece thickness enables precise control over the welding process and ensures reliable and efficient performance in energy storage spot welding applications.