Energy storage spot welding machines are widely used in various industries for their ability to create strong and reliable welds. Three critical parameters in the welding process are pre-pressure, pressure, and hold time. Understanding the significance of these parameters and their proper adjustment is essential to ensure optimal weld quality. This article provides a comprehensive explanation of pre-pressure, pressure, and hold time in energy storage spot welding machines, highlighting their roles and the factors that influence their adjustment.
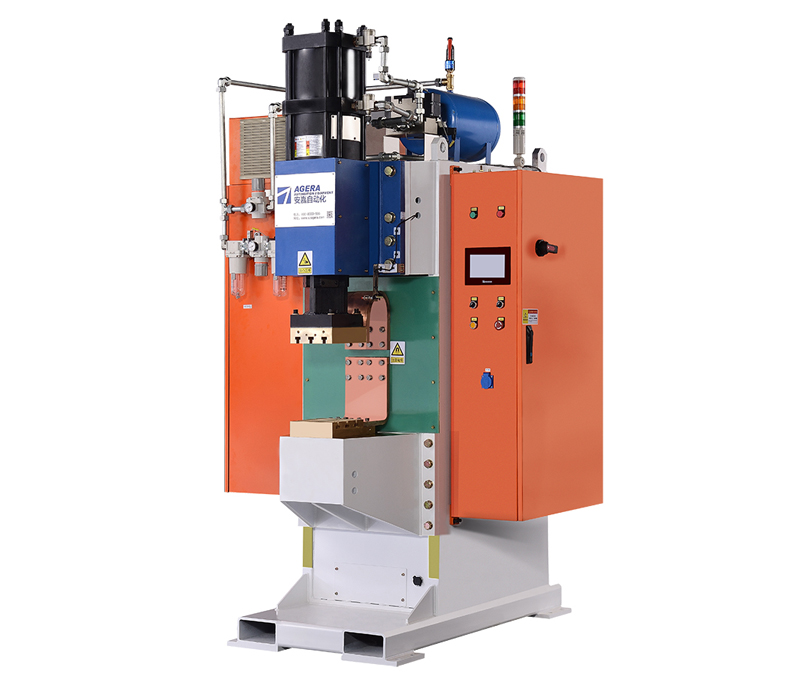
- Pre-Pressure: Pre-pressure, also known as squeeze time, refers to the initial application of electrode force on the workpieces before the welding current is activated. The purpose of pre-pressure is to establish a stable and consistent contact between the electrodes and the workpieces, ensuring proper alignment and minimizing any air gaps or surface contaminants. Pre-pressure helps create a reliable electrical and thermal connection between the electrodes and the workpieces, leading to improved weld quality. The duration of pre-pressure depends on factors such as workpiece material, thickness, and joint configuration.
- Pressure: Pressure, also known as welding time or welding current time, is the period during which the welding current flows through the workpieces, generating the necessary heat for fusion. The pressure should be applied with sufficient force to ensure proper material deformation and achieve a strong bond between the workpieces. The duration of pressure is determined by factors such as workpiece material, thickness, desired weld strength, and welding machine capabilities. It is important to balance the pressure duration to avoid excessive heat buildup and potential workpiece damage while ensuring complete fusion of the joint.
- Hold Time: Hold time, also referred to as post-pressure or forge time, is the period following the termination of the welding current. During this time, the pressure is maintained on the workpieces to allow for solidification and cooling of the weld. Hold time is crucial for the formation of a strong metallurgical bond and the prevention of weld defects such as cracks or porosity. The duration of hold time depends on factors such as workpiece material, joint configuration, and cooling requirements. Adequate hold time allows the weld to solidify and attain its maximum strength before releasing the pressure.
Factors Influencing Adjustment: Several factors influence the adjustment of pre-pressure, pressure, and hold time in energy storage spot welding machines. These include:
- Workpiece material and thickness: Different materials and thicknesses require varying levels of force and duration for proper fusion.
- Joint configuration: Complex or dissimilar joints may require specific adjustments to ensure uniform heat distribution and sufficient material deformation.
- Weld quality requirements: Desired weld strength, aesthetics, and specific industry standards influence the selection and adjustment of these parameters.
- Machine capabilities: The welding machine’s power output, control features, and available settings play a role in determining the optimal values for pre-pressure, pressure, and hold time.
Precise adjustment of pre-pressure, pressure, and hold time in energy storage spot welding machines is crucial for achieving high-quality and reliable welds. Understanding the roles and significance of these parameters, along with the factors influencing their adjustment, allows operators to optimize the welding process for different workpieces and joint configurations. By carefully adjusting pre-pressure, pressure, and hold time, welders can ensure proper material deformation, strong metallurgical bonds, and the avoidance of weld defects, resulting in robust and durable welds.