The design of welding fixtures and devices plays a crucial role in the performance and efficiency of Capacitor Discharge (CD) spot welding machines. Welding fixtures are essential for ensuring proper alignment, positioning, and clamping of workpieces during the welding process. This article outlines key considerations for designing effective welding fixtures and devices in CD spot welding machines.
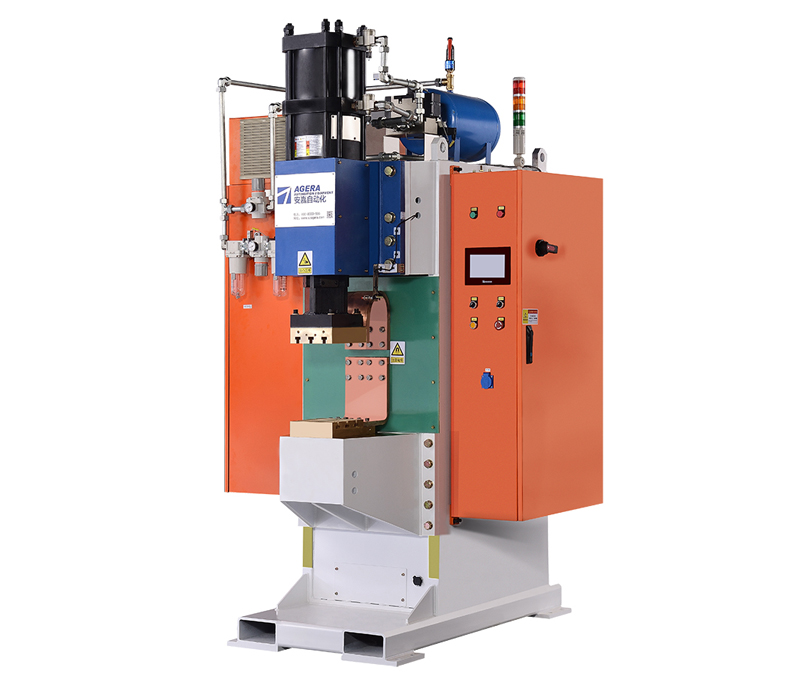
- Workpiece Alignment and Clamping: Proper alignment and secure clamping of workpieces are essential to achieving consistent and high-quality welds. Design fixtures that allow easy adjustment and secure clamping of workpieces to prevent misalignment and movement during welding.
- Electrode Placement and Contact: The positioning of electrodes is critical for ensuring optimal energy transfer and uniform weld quality. Design fixtures that facilitate accurate electrode placement, maintain proper electrode contact with the workpieces, and prevent electrode wear.
- Material Compatibility: Choose materials for the fixtures and devices that are compatible with the workpiece materials and welding conditions. Consider factors such as electrical conductivity, thermal expansion, and heat resistance.
- Cooling and Heat Dissipation: In high-volume welding operations, heat buildup in fixtures and devices can affect their longevity and performance. Integrate cooling mechanisms such as water circulation or air cooling to dissipate excess heat and maintain consistent welding conditions.
- Accessibility and Ease of Use: Design fixtures that are user-friendly and allow easy access for loading and unloading workpieces. Consider ergonomic factors to ensure operators can efficiently use the fixtures without strain.
- Durability and Maintenance: Welding fixtures should be robust and durable to withstand repeated use and mechanical stresses. Incorporate features that facilitate easy maintenance and replacement of worn components.
- Automation Compatibility: For automated welding systems, design fixtures that can be easily integrated with robotic arms or other automated equipment. Ensure compatibility with sensors and positioning devices for precise alignment.
- Welding Process Variability: Account for variations in workpiece dimensions, shapes, and tolerances. Design fixtures that can accommodate different part geometries and ensure consistent electrode contact.
- Safety Measures: Include safety features such as interlocks, shielding, and insulation to protect operators from electrical hazards and welding sparks.
Effective design of welding fixtures and devices is a critical aspect of optimizing the performance and efficiency of Capacitor Discharge spot welding machines. A well-designed fixture ensures accurate alignment, secure clamping, and proper electrode contact, resulting in consistent and high-quality welds. By considering factors such as workpiece alignment, material compatibility, cooling mechanisms, ease of use, and durability, manufacturers can create fixtures that enhance productivity and maintain weld quality.