Sparks during the nut spot welding process can occur due to various factors and may have undesirable effects on the welding quality and safety. It is important to understand the causes of sparks and implement appropriate measures to prevent or mitigate them. This article addresses the issue of sparks during nut spot welding and provides practical solutions to deal with this challenge effectively.
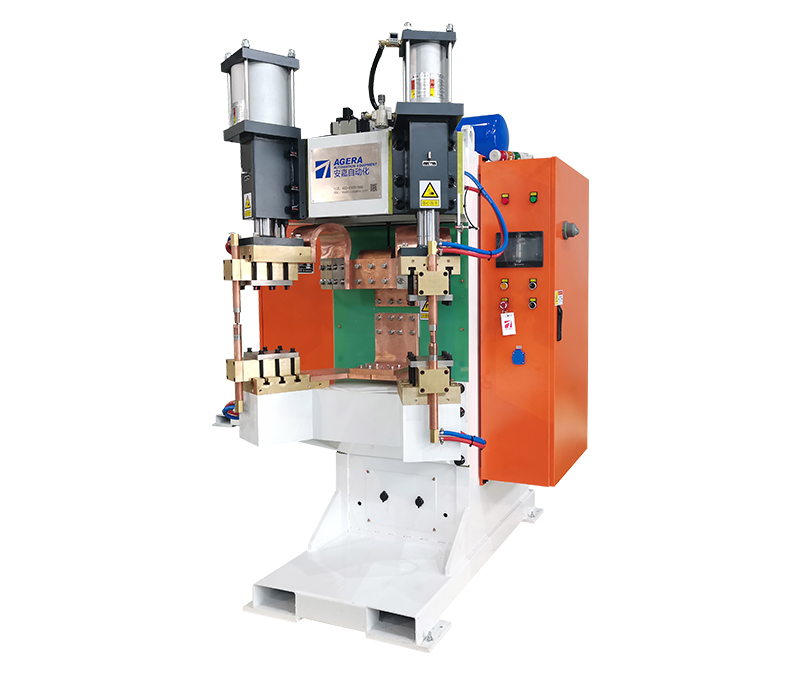
- Causes of Sparks: Sparks during nut spot welding can be caused by several factors, including: a. Contamination: Presence of oil, grease, or other contaminants on the workpieces or electrodes can lead to sparking. b. Poor Electrode Contact: Insufficient or uneven electrode contact with the workpieces can result in arcing and sparks. c. Incorrect Pressure: Inadequate pressure between the electrodes and workpieces can cause sparking. d. Incorrect Electrode Alignment: Misalignment of the electrodes can lead to sparks during the welding process.
- Prevention and Mitigation: To address the issue of sparks during nut spot welding, the following measures can be taken: a. Cleanliness: Ensure proper cleaning of the workpieces and electrodes to remove any contaminants that may cause sparks. b. Electrode Maintenance: Regularly inspect and clean the electrodes to ensure optimal surface condition and proper contact with the workpieces. c. Pressure Adjustment: Adjust the electrode pressure to ensure sufficient and uniform contact with the workpieces, reducing the likelihood of sparking. d. Electrode Alignment: Verify and adjust the electrode alignment to ensure accurate and consistent contact with the workpieces, minimizing the chances of sparking.
- Monitoring and Quality Control: Implementing real-time monitoring and quality control measures can help detect sparks during the welding process. These include: a. Visual Inspection: Train operators to visually inspect the welding process for any signs of sparks and take immediate action if observed. b. Monitoring Systems: Utilize advanced monitoring systems that can detect and alert operators in real-time when sparks occur. c. Quality Checks: Perform regular quality checks on welded joints to identify any defects associated with sparking, ensuring adherence to quality standards.
- Operator Training and Awareness: Proper training and awareness programs for operators are crucial in preventing and addressing sparking issues. Operators should be educated on the causes of sparks, the importance of maintaining clean electrodes, and the significance of proper electrode contact and alignment. Additionally, they should be trained on how to adjust parameters and take corrective actions when sparks occur.
Sparks during nut spot welding can be effectively managed by understanding the causes and implementing preventive measures. Maintaining cleanliness, proper electrode contact and alignment, and monitoring systems can significantly reduce the occurrence of sparks. By following these guidelines and providing adequate training to operators, the welding process can be performed safely and efficiently, resulting in high-quality welds and minimizing the risk of defects.