Regular maintenance and care are essential for ensuring the optimal performance and longevity of nut projection welding machines. Proper maintenance practices help prevent breakdowns, minimize downtime, and maximize productivity. In this article, we will provide an overview of the key maintenance and care practices for nut projection welding machines, highlighting their importance and benefits.
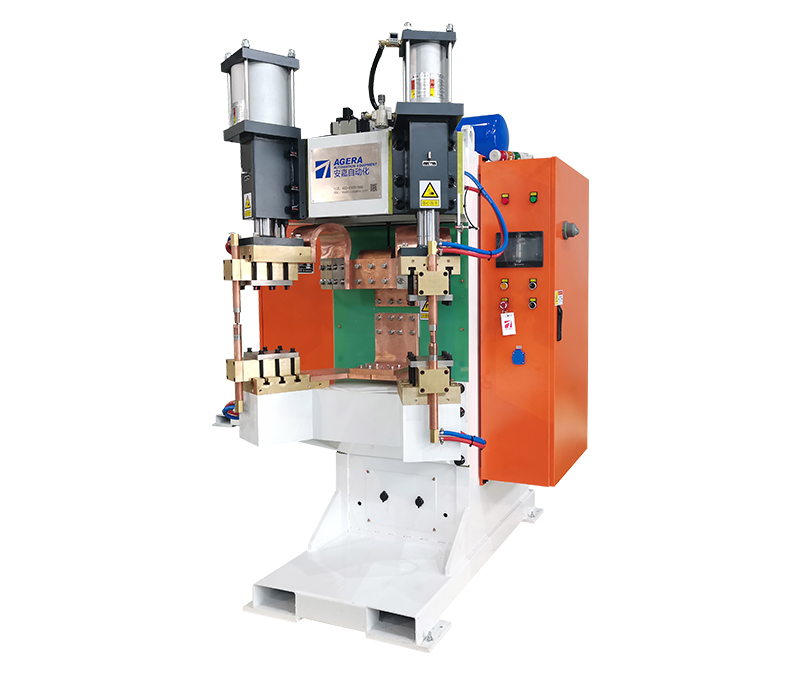
- Cleaning: Regular cleaning is crucial to keep nut projection welding machines in good working condition. Remove dust, debris, and any metal shavings from the machine’s surface, components, and electrical connections. Use compressed air, brushes, or vacuum cleaners to clean hard-to-reach areas. Clean and inspect the electrodes, replacing them if necessary. A clean machine promotes efficient operation and reduces the risk of contamination or damage to sensitive parts.
- Lubrication: Proper lubrication is vital for the smooth functioning of moving parts and mechanisms in nut projection welding machines. Follow the manufacturer’s guidelines to identify the lubrication points and use the recommended lubricants. Regularly inspect and lubricate components such as bearings, slides, and pivot points to prevent excessive friction, wear, and corrosion. Lubrication enhances machine performance, reduces energy consumption, and extends the lifespan of critical components.
- Electrical System Inspection: Regularly inspect the electrical system of nut projection welding machines to ensure safe and reliable operation. Check for loose or damaged electrical connections, frayed cables, and worn-out insulation. Verify that all electrical components, such as relays, switches, and control panels, are functioning correctly. Periodically calibrate the machine’s voltage and current settings to maintain accurate welding parameters.
- Cooling System Maintenance: Many nut projection welding machines are equipped with cooling systems to prevent overheating. Check the coolant level regularly and ensure proper circulation. Clean or replace the filters to prevent clogging and ensure efficient heat dissipation. Inspect the cooling pipes and hoses for leaks or damage. Maintaining a well-functioning cooling system helps prevent component overheating, extends their lifespan, and ensures consistent welding performance.
- Regular Calibration and Testing: Periodic calibration and testing of nut projection welding machines are essential to maintain accurate welding parameters and high-quality welds. Use calibrated measuring instruments to verify the machine’s welding force, electrode alignment, and weld quality. Conduct test welds on sample materials to assess the machine’s performance and make any necessary adjustments. Regular calibration and testing promote consistent weld quality and help identify potential issues early on.
Regular maintenance and care are critical for the reliable and efficient operation of nut projection welding machines. By implementing proper cleaning practices, ensuring appropriate lubrication, inspecting the electrical system, maintaining the cooling system, and performing regular calibration and testing, manufacturers can optimize the machine’s performance, minimize downtime, and ensure consistent weld quality. Following a comprehensive maintenance plan will extend the machine’s lifespan, enhance productivity, and maximize the return on investment.