Resistance welding is a widely used manufacturing process, relied upon for its efficiency and reliability in joining metals. To ensure the quality and safety of welded products, it is imperative to closely monitor the welding current during the process. In this article, we will explore the importance of current monitoring in resistance welding machines and how this function contributes to better welds and overall process control.
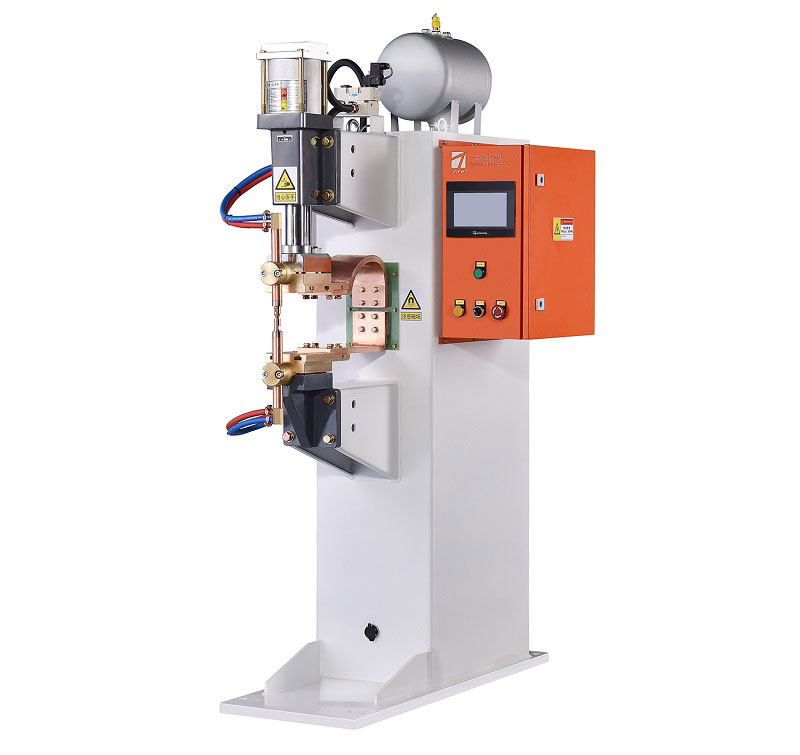
Importance of Current Monitoring:
- Quality Assurance: Welding current plays a pivotal role in determining the quality of the weld joint. Any variations or anomalies in the current can result in defects such as weak welds, cracks, or incomplete penetration. By monitoring the current in real-time, operators can promptly identify and rectify issues, ensuring that the final product meets the required quality standards.
- Process Stability: Maintaining a consistent welding current is essential for process stability. Variations in current can lead to inconsistent welds, which can be problematic in industries where precision and uniformity are crucial. The ability to monitor and control current ensures that each weld is executed with precision, resulting in reliable and repeatable outcomes.
- Preventing Overheating: Excessive current can cause the welding equipment to overheat, potentially damaging the machinery or even causing safety hazards. Current monitoring serves as a protective measure by triggering alarms or automatically adjusting the current if it exceeds safe limits, thereby safeguarding both the equipment and the operators.
Key Features of Current Monitoring in Resistance Welding Machines:
- Real-Time Data: Modern resistance welding machines are equipped with sensors that continuously measure and display the welding current in real-time. This data allows operators to monitor the process closely and make necessary adjustments as required.
- Data Logging: Some machines are equipped with data logging capabilities, which record the welding current data for each weld. This historical data is invaluable for quality control and process optimization, as it enables the identification of trends or patterns that may indicate issues with the welding process.
- Automatic Control: Advanced welding machines can automatically adjust the current during the welding process to maintain optimal conditions. This automation reduces the reliance on operator skill and helps ensure consistently high-quality welds.
- Alarms and Notifications: Current monitoring systems can be programmed to trigger alarms or notifications when the current deviates from the set parameters. This immediate feedback allows for swift action to address any anomalies.
In conclusion, current monitoring is a critical function in resistance welding machines that contributes significantly to the quality, safety, and efficiency of the welding process. With real-time data, historical records, and automated control features, modern welding machines offer enhanced capabilities for precise and reliable welds. As manufacturing demands continue to evolve, the role of current monitoring in resistance welding will only become more indispensable.