Butt welding machines play a crucial role in various industries, facilitating the joining of metals to create strong and durable welds. To ensure the success of welding operations, precise control over the welding process is paramount. This article explores the essential control requirements for butt welding machines and their significance in achieving optimal weld results.
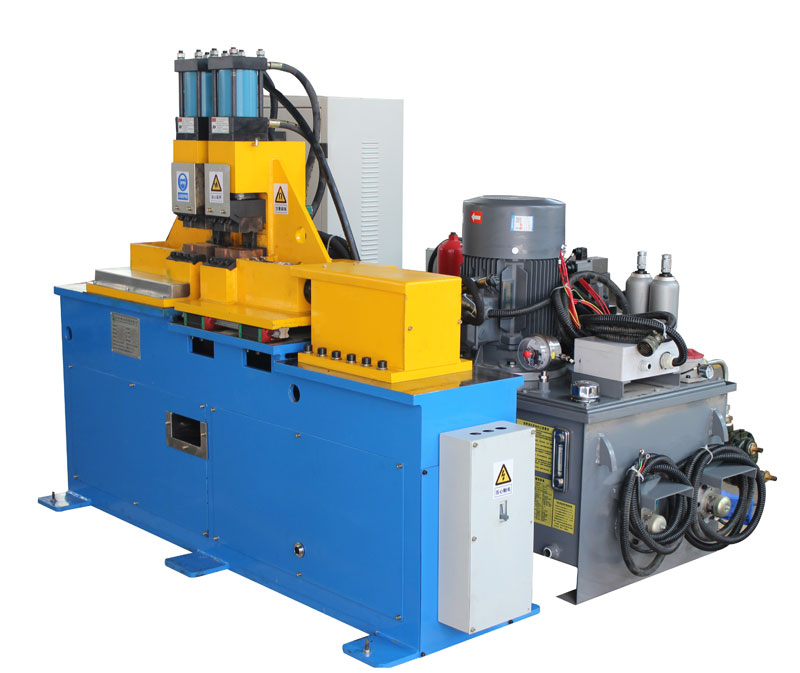
- Precise Current and Voltage Control: Accurate control of welding current and voltage is essential for producing consistent and high-quality welds. Butt welding machines must be equipped with advanced control systems that maintain stable current and voltage levels throughout the welding process, ensuring uniform fusion and minimizing defects.
- Control of Welding Time: Controlling the duration of the welding process is critical for achieving proper fusion and penetration. Butt welding machines should allow for precise adjustment of the welding time to match the requirements of different materials and joint configurations.
- Adaptive Welding Control: In some welding applications, material properties may vary, leading to different welding conditions. Butt welding machines with adaptive control capabilities can automatically adjust welding parameters based on real-time feedback, optimizing weld quality and reducing the need for manual interventions.
- Electrode Force Control: Appropriate electrode force is crucial for maintaining proper contact between the workpieces during welding. Butt welding machines should feature control mechanisms that allow for consistent and adjustable electrode force, ensuring consistent weld quality across various workpiece thicknesses.
- Temperature and Heat Control: Monitoring and controlling heat input during the welding process is vital to avoid overheating or underheating of the workpiece. Advanced temperature and heat control systems in butt welding machines help prevent material distortion and ensure reliable welds.
- Welding Speed Control: The welding speed can influence the weld characteristics, including bead appearance and heat-affected zone. Butt welding machines with speed control mechanisms enable operators to optimize the welding process for different applications and materials.
- Real-Time Monitoring and Data Logging: Integrating real-time monitoring and data logging features in butt welding machines allows operators to track welding parameters and performance. This information facilitates process analysis, quality control, and process optimization.
- Safety Interlocks and Emergency Stop: Safety is of utmost importance in welding operations. Butt welding machines must be equipped with safety interlocks and emergency stop features to protect operators and prevent equipment damage in case of any abnormal events.
In conclusion, butt welding machines must meet stringent control requirements to ensure the success of welding operations. Precise control over welding current, voltage, time, and electrode force is essential for achieving consistent and high-quality welds. Adaptive control capabilities, real-time monitoring, and safety features further enhance the welding process’s efficiency and reliability. By investing in butt welding machines that meet these control requirements, manufacturers can produce robust and reliable welds, leading to improved productivity and customer satisfaction.