Proper maintenance and regular cleaning of energy storage welding machines are essential for ensuring their optimal performance and longevity. This article aims to explore various cleaning methods that can be employed to keep these machines in pristine condition. By understanding the cleaning techniques, users can effectively remove debris, contaminants, and residues that may accumulate during the welding process, thus maintaining the efficiency and reliability of their energy storage welding machines.
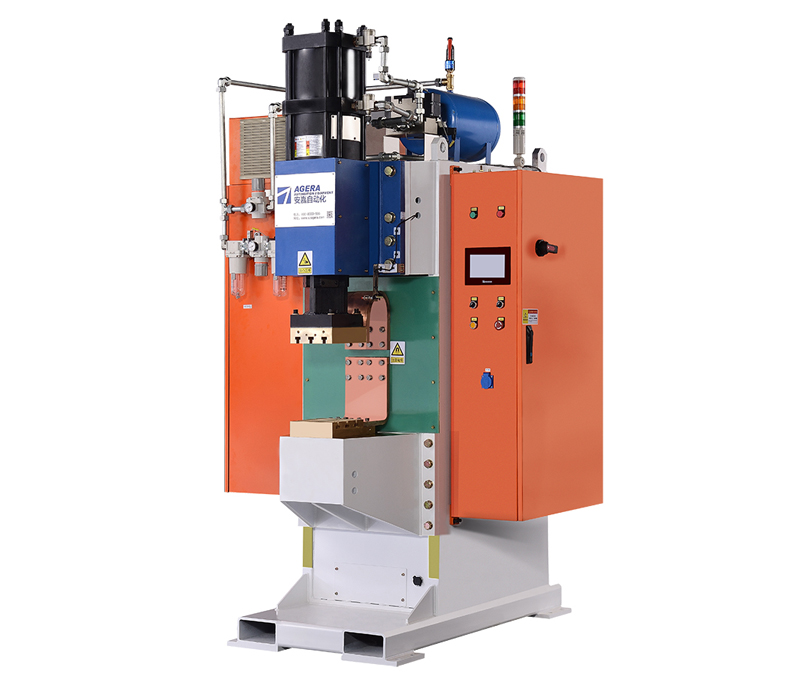
- External Cleaning: The external surfaces of energy storage welding machines can accumulate dust, dirt, and grease over time. Cleaning the exterior not only enhances the machine’s appearance but also prevents the build-up of debris that can potentially affect its performance. Common cleaning methods for the exterior include wiping with a soft cloth, using mild detergent solutions, or using specialized machine cleaning agents. It is important to follow the manufacturer’s instructions regarding the appropriate cleaning agents and methods to avoid damaging the machine’s sensitive components.
- Cooling System Cleaning: Energy storage welding machines often feature cooling systems to prevent overheating during prolonged operation. These systems can accumulate mineral deposits and impurities that may impede cooling efficiency. To clean the cooling system, users can flush it with a mixture of water and mild cleaning agents, ensuring thorough removal of any debris or sediments. It is crucial to refer to the machine’s user manual or consult with the manufacturer for specific cleaning instructions related to the cooling system.
- Electrode Cleaning: The electrodes used in energy storage welding machines can become contaminated with weld spatter, oxidation, or other residues, affecting their performance and welding quality. Cleaning the electrodes involves removing these contaminants to maintain proper electrical conductivity and ensure consistent welds. Various methods can be employed, such as using a wire brush, sandpaper, or dedicated electrode cleaning solutions. Care should be taken to avoid excessive abrasion that may shorten the electrode’s lifespan.
- Internal Cleaning: Periodic internal cleaning of energy storage welding machines is necessary to remove accumulated dust, metal particles, and other contaminants that can affect internal components’ functionality. However, internal cleaning should only be performed by trained professionals or authorized service technicians, as it involves accessing sensitive parts of the machine and requires expertise to prevent damage.
- Regular Maintenance: In addition to cleaning, regular maintenance procedures recommended by the manufacturer should be followed. This may include lubrication of moving parts, inspection of electrical connections, and calibration of settings. Adhering to a maintenance schedule ensures that the energy storage welding machine operates at its optimum level and reduces the risk of unexpected breakdowns.
Cleaning and maintenance are vital aspects of keeping energy storage welding machines in optimal condition. By implementing appropriate cleaning methods for the external surfaces, cooling system, electrodes, and conducting regular maintenance procedures, users can prolong the lifespan of their machines and ensure consistent welding performance. It is crucial to consult the manufacturer’s guidelines and seek professional assistance when necessary to maintain the integrity and reliability of the energy storage welding machine.