Butt welding machines are distinguished by unique process characteristics that make them a preferred choice for joining metals in various industrial applications. Understanding these distinct features is essential for welders and professionals in the welding industry. This article explores the key characteristics of the butt welding machine process, shedding light on its significance and the benefits it offers for achieving strong and efficient welds.
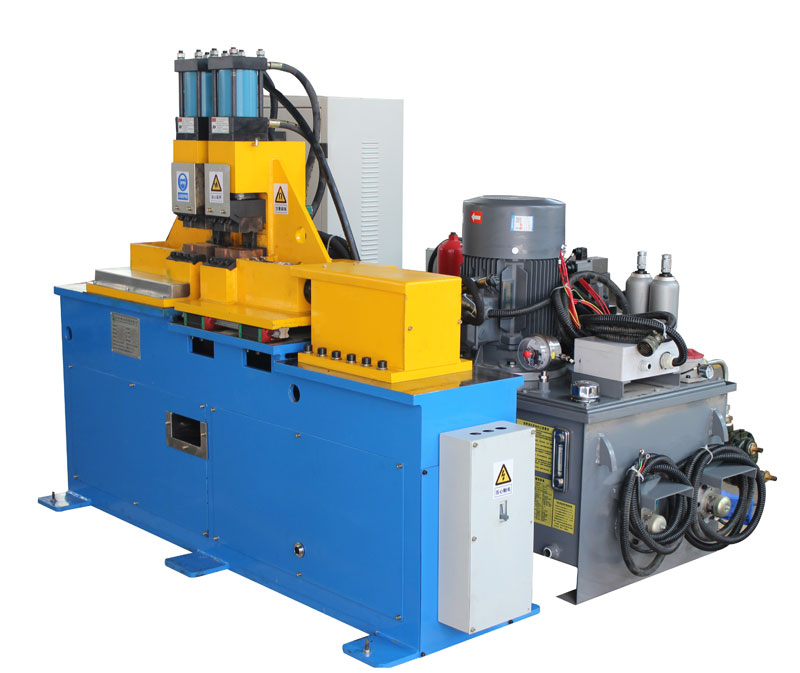
- High Fusion Integrity: One of the prominent characteristics of the butt welding machine process is its ability to achieve high fusion integrity. By applying precise welding parameters and ensuring proper alignment of workpieces, the welding process generates a uniform and robust weld joint with excellent fusion.
- Minimal Material Distortion: The butt welding machine process minimizes material distortion during welding. Proper heat control and consistent electrode withdrawal speed contribute to reduced thermal impact on the base metals, resulting in minimal distortion or deformation of the workpieces.
- Strong and Durable Welds: The butt welding machine process produces welds with superior strength and durability. The uniform fusion and minimal heat-affected zone contribute to welds that exhibit high mechanical properties, making them suitable for critical structural applications.
- Versatility in Material Compatibility: The process characteristics of butt welding machines allow for versatility in material compatibility. Whether joining similar or dissimilar metals, the butt welding process can accommodate various material combinations, providing a wide range of welding possibilities.
- Efficient Welding Speed: Butt welding machines offer efficient welding speed, contributing to increased productivity in industrial settings. With precise control over welding parameters, operators can achieve high-quality welds within shorter time frames.
- Minimized Welding Debris: The butt welding machine process significantly reduces spatter and welding debris compared to other welding techniques. This feature ensures a cleaner working environment and reduces post-weld cleanup efforts.
- Consistent Weld Quality: Consistency is a hallmark of butt welding machine process characteristics. By adhering to proper welding procedures, workpiece preparation, and control of welding parameters, the process consistently delivers welds with reliable quality.
- Welding Automation Compatibility: The characteristics of butt welding machines make them compatible with welding automation and robotic systems. Integrating automation streamlines welding processes, increases repeatability, and enhances overall efficiency.
In conclusion, the butt welding machine process boasts distinctive characteristics that set it apart as a versatile and efficient welding technique. High fusion integrity, minimal material distortion, strong and durable welds, versatility in material compatibility, efficient welding speed, minimized welding debris, consistent weld quality, and compatibility with welding automation make butt welding machines an indispensable tool in the welding industry. By harnessing these process characteristics and emphasizing best practices, welders can achieve outstanding welding outcomes, meet diverse industrial demands, and contribute to advancements in metal joining technology. The butt welding machine process continues to play a crucial role in numerous applications, bridging the gap between innovation and reliable metal fabrication processes.