Welding electrodes play a crucial role in energy storage spot welding machines, facilitating the transfer of electrical current and generating the necessary heat for welding. However, over time, electrodes can experience wear and degradation, affecting their performance and weld quality. Understanding the causes of electrode wear is essential for implementing appropriate maintenance and replacement strategies. This article explores the factors contributing to electrode wear in energy storage spot welding machines, shedding light on the underlying reasons and potential solutions.
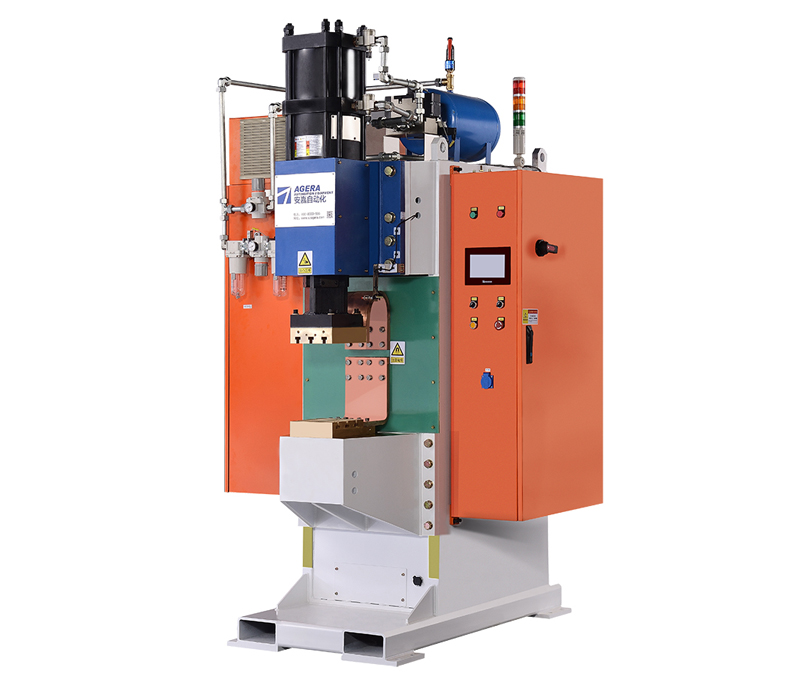
- Electrical Resistance and Heat Generation: During the welding process, high electrical currents pass through the electrodes, generating heat at the contact points with the workpieces. This heat can cause localized temperature elevation, leading to thermal expansion and contraction of the electrodes. The repeated heating and cooling cycles induce stress on the electrode surface, resulting in gradual wear, deformation, and material loss. Higher welding currents and longer welding durations can exacerbate this wear process.
- Mechanical Friction and Pressure: Welding electrodes are subjected to mechanical forces during the welding operation. The pressure applied to the electrodes, along with any relative movement or vibration between the electrodes and the workpieces, can cause friction and rubbing. This mechanical interaction can lead to surface abrasion, erosion, and even the formation of cracks or chips on the electrode surface. Factors such as excessive force, improper alignment, or the presence of contaminants can accelerate this wear mechanism.
- Electrochemical Reactions: In some welding processes, particularly those involving dissimilar metals or corrosive environments, electrochemical reactions can occur at the electrode surface. These reactions can lead to electrode corrosion, pitting, or the formation of oxides. Corrosion weakens the electrode material, making it more susceptible to wear and degradation. Factors such as inadequate electrode material selection or improper shielding gas can contribute to accelerated electrochemical wear.
- Contaminants and Oxidation: Contaminants, such as dirt, grease, or residual flux, can accumulate on the electrode surface over time. These contaminants can interfere with the electrical and thermal conductivity of the electrodes, causing localized hot spots, uneven heating, and poor weld quality. Additionally, exposure to oxygen in the welding environment can lead to oxidation of the electrode surface, forming oxides that reduce conductivity and increase resistance, ultimately affecting the performance and lifespan of the electrodes.
Mitigation Strategies: To address electrode wear in energy storage spot welding machines, several strategies can be employed:
- Regular inspection and cleaning of electrodes to remove contaminants and ensure optimal contact.
- Proper electrode material selection based on the welding application and workpiece materials.
- Implementing appropriate shielding gases or coatings to minimize oxidation and electrochemical reactions.
- Optimizing welding parameters, such as current, duration, and pressure, to minimize excessive heat and mechanical stress on the electrodes.
- Timely replacement of worn electrodes to maintain consistent weld quality and prevent damage to the workpieces.
Conclusion: Understanding the causes of electrode wear in energy storage spot welding machines is vital for maintaining efficient and high-quality welding operations. By considering factors such as electrical resistance, mechanical friction, electrochemical reactions, and contaminants, operators can implement preventive measures and mitigation strategies to prolong electrode lifespan and ensure reliable weld performance. Regular maintenance, proper material selection, and adherence to recommended welding parameters are key to minimizing electrode wear and maximizing the longevity of electrodes in energy storage spot welding machines.