Nut projection welding is a widely used process for joining nuts to metal workpieces. One of the challenges faced in this process is the rapid wear of electrodes. In this article, we will explore the factors that contribute to electrode wear in nut projection welding and discuss potential solutions to mitigate this issue.
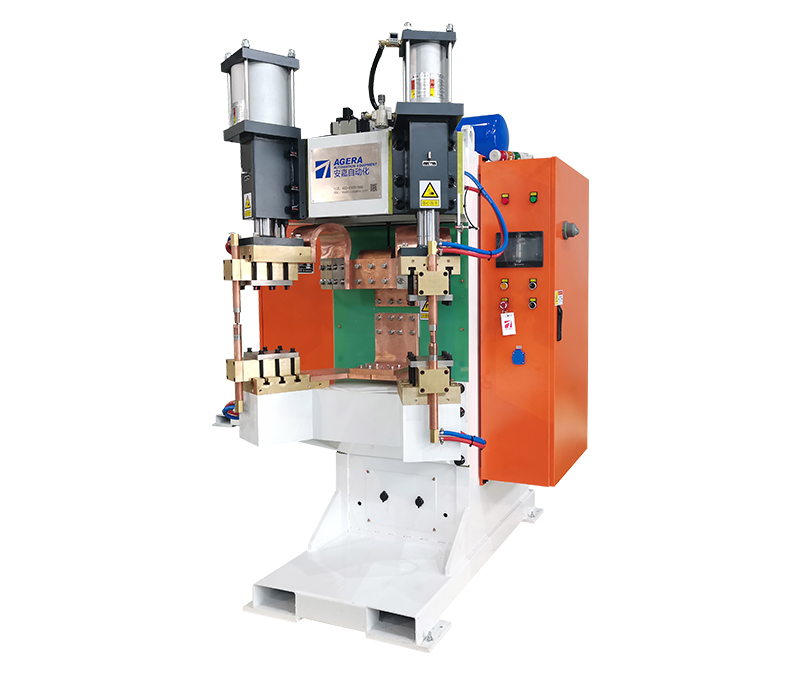
- High Current and Pressure: The combination of high welding current and pressure during nut projection welding can lead to increased electrode wear. The intense heat generated at the contact points between the electrode and the workpiece causes material transfer and erosion of the electrode surface. This effect is more pronounced when working with hard or abrasive materials.
- Insufficient Cooling: Inadequate cooling of the electrode can also accelerate wear. The repeated heating and cooling cycles during welding generate significant thermal stress on the electrode. Insufficient cooling can result in overheating, which softens the electrode material and causes deformation or accelerated erosion.
- Contaminants and Oxidation: Contaminants, such as oil, grease, or dirt, on the workpiece or electrode surface can contribute to electrode wear. These contaminants can react with the high temperatures during welding, leading to accelerated oxidation and corrosion of the electrode. Oxidation weakens the electrode material and promotes electrode degradation.
- Improper Electrode Material Selection: Choosing an inappropriate electrode material for the specific application can also lead to rapid wear. Factors such as the composition and hardness of the workpiece material, as well as the welding current and pressure, should be considered when selecting the electrode material. Incompatible electrode materials may not withstand the welding conditions, resulting in premature wear.
Solutions to Mitigate Electrode Wear: To reduce electrode wear in nut projection welding, several measures can be taken:
- Optimize Welding Parameters: Adjusting the welding current, pressure, and cooling rate to optimal levels can help minimize electrode wear. Finding the right balance between achieving a strong weld and reducing electrode stress is essential.
- Implement Proper Cooling Systems: Ensuring effective cooling of the electrode, such as using water-cooled electrode holders or cooling circuits, can help dissipate heat and maintain the electrode’s integrity.
- Maintain Clean Surfaces: Thoroughly cleaning the workpiece and electrode surfaces before welding can prevent the accumulation of contaminants that contribute to electrode wear. Regular maintenance and cleaning of the equipment are essential.
- Select Suitable Electrode Materials: Choosing electrode materials with higher hardness, resistance to oxidation, and wear resistance can extend the electrode’s lifespan. Consultation with suppliers and experts can aid in selecting the most suitable electrode material for the specific application.
Understanding the factors that contribute to rapid electrode wear in nut projection welding is crucial for improving the welding process’s efficiency and cost-effectiveness. By optimizing welding parameters, implementing proper cooling systems, maintaining clean surfaces, and selecting appropriate electrode materials, manufacturers can minimize electrode wear and achieve reliable and long-lasting welds in nut projection welding operations.