Resistance spot welding is a widely used technique for joining metal parts in various industries. It involves the use of a specialized machine that creates strong, reliable welds by applying heat and pressure to the workpieces. To ensure successful welds, it is crucial to understand and follow the basic operations of a resistance spot welding machine. In this article, we will walk you through these fundamental steps.
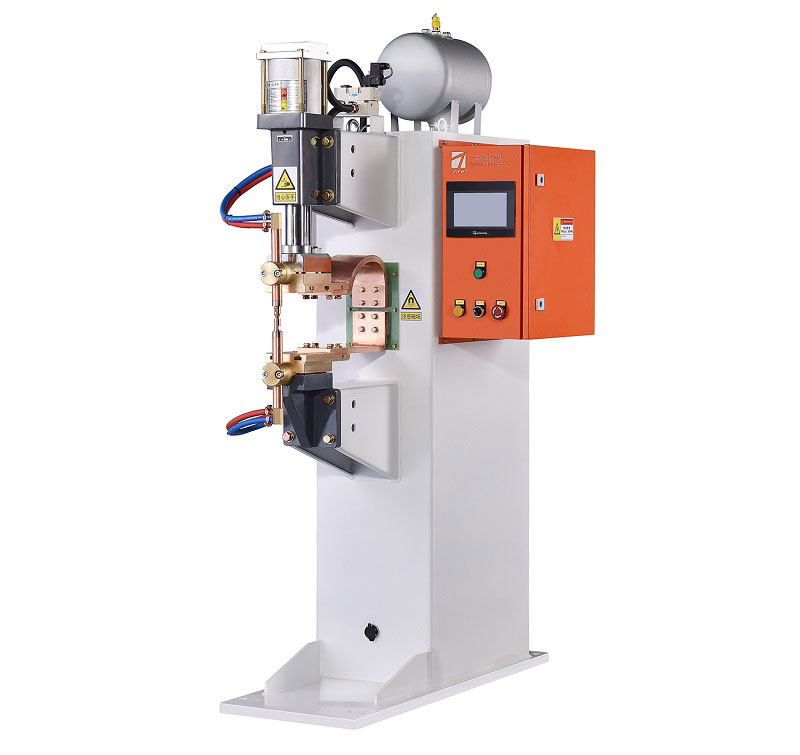
- Machine Setup: Before starting any welding operation, ensure that the welding machine is properly set up. This includes checking the power supply, electrode alignment, and the condition of the welding electrodes. Make sure the machine is grounded to prevent electrical hazards.
- Material Preparation: Prepare the materials to be welded by cleaning them thoroughly. Remove any dirt, rust, or contaminants from the surfaces to ensure a clean and strong weld. Proper material preparation is essential for achieving high-quality welds.
- Adjusting Welding Parameters: Different materials and thicknesses require specific welding parameters. These parameters include welding current, welding time, and electrode force. Consult the machine’s manual or welding procedure specifications to determine the appropriate settings for your job.
- Positioning the Workpieces: Position the workpieces to be welded in the welding machine’s electrodes. Proper alignment and positioning are crucial for achieving strong, consistent welds. Use jigs or fixtures if necessary to ensure accurate placement.
- Welding Operation: Once the workpieces are correctly positioned, initiate the welding cycle by pressing the machine’s start button. The machine will apply pressure and electrical current to create a weld. Monitor the welding process to ensure that it proceeds smoothly.
- Cooling Time: After the welding cycle is complete, allow sufficient time for the weld to cool. Cooling time may vary depending on the material and thickness. Avoid moving or disturbing the welded parts during this phase to prevent defects.
- Inspecting the Weld: Inspect the weld visually and, if necessary, perform non-destructive testing to ensure the quality of the weld. Look for any signs of defects such as cracks, porosity, or incomplete fusion. A well-executed weld should be smooth and uniform.
- Post-Weld Cleaning and Finishing: After confirming the weld’s quality, clean any residual flux or slag from the weld area. Depending on the application, you may need to perform additional finishing operations such as grinding or polishing to achieve the desired surface quality.
- Documentation: Maintain proper documentation of the welding process, including the welding parameters used, inspection results, and any necessary quality control records. This documentation is crucial for traceability and quality assurance.
- Safety Precautions: Throughout the entire welding process, prioritize safety. Wear appropriate personal protective equipment (PPE), follow safety guidelines, and be aware of potential hazards associated with welding operations.
In conclusion, mastering the basic operations of a resistance spot welding machine is essential for producing high-quality welds and ensuring the safety of operators. By following these steps and adhering to best practices, you can achieve consistent and reliable results in your welding projects.