Nut spot welding machines are widely used in various industries for their efficient and reliable joining capabilities. In addition to the key components, there are several auxiliary components that can enhance the performance of these machines. This article provides an overview of the auxiliary components that contribute to improved functionality and performance of nut spot welding machines.
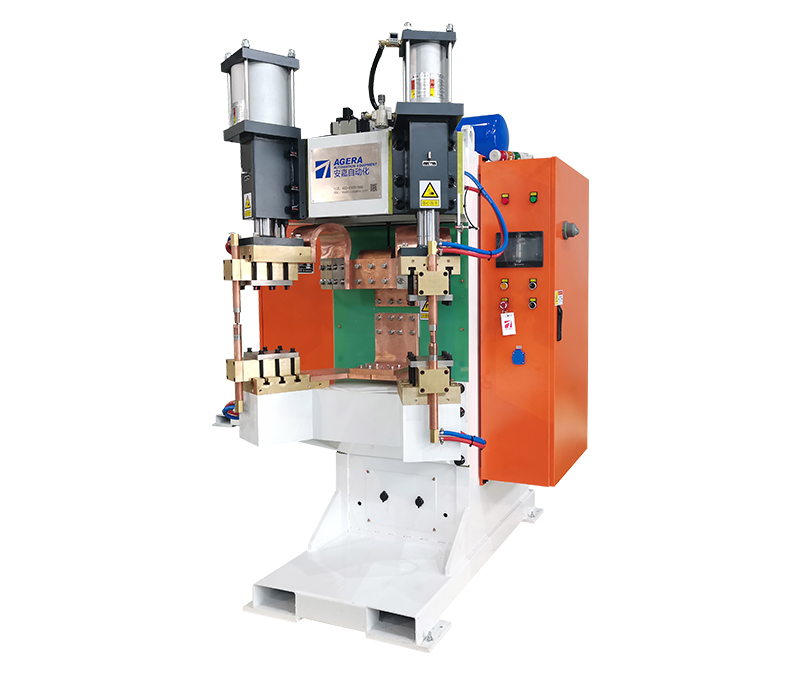
- Electrode Dressing Equipment: Electrode dressing equipment is used to maintain the shape and condition of the welding electrodes. It helps remove any built-up material or contaminants on the electrode tips, ensuring optimal electrical conductivity and efficient heat transfer during the welding process. Properly dressed electrodes result in consistent weld quality and prolonged electrode life.
- Electrode Force Monitoring System: An electrode force monitoring system is designed to measure and maintain the optimal pressure applied by the electrodes during the welding operation. It ensures consistent and uniform pressure, which is crucial for achieving reliable and high-quality welds. This system provides real-time feedback and adjustments to maintain the desired electrode force.
- Welding Current Monitoring Device: A welding current monitoring device allows operators to monitor the welding current during the welding process. It provides real-time information about the current levels, enabling operators to ensure that the desired current is being delivered for each weld. This monitoring device helps identify any deviations or inconsistencies in the welding process, facilitating prompt adjustments if needed.
- Welding Quality Inspection Tools: Welding quality inspection tools, such as visual inspection systems or non-destructive testing equipment, are used to assess the quality and integrity of the welds produced by the nut spot welding machine. These tools can detect defects, such as cracks or insufficient fusion, and ensure compliance with specified welding standards. Quality inspection tools help identify potential issues early on and enable necessary corrective actions.
- Programmable Logic Controller (PLC): A programmable logic controller is an advanced control system that allows for precise and automated control of various welding parameters. It offers flexibility in programming and adjusting welding parameters, such as current, time, and pressure, based on specific requirements. A PLC enhances the repeatability, accuracy, and consistency of the welding process, resulting in improved overall performance.
- Welding Data Management System: A welding data management system records and stores essential welding parameters and results for each weld. It allows for efficient documentation and traceability, facilitating quality control and process optimization. By analyzing the collected data, operators can identify trends, optimize welding parameters, and continuously improve the performance of the nut spot welding machine.
In addition to the key components, several auxiliary components play a vital role in enhancing the performance of nut spot welding machines. Electrode dressing equipment, electrode force monitoring systems, welding current monitoring devices, welding quality inspection tools, programmable logic controllers, and welding data management systems contribute to improved functionality, quality control, and productivity. Incorporating these auxiliary components can help manufacturers achieve higher weld quality, efficiency, and reliability in nut spot welding applications.