In nut projection welding, the selection of appropriate electrode types is crucial for achieving optimal welding results. Different electrode types offer unique advantages and characteristics that suit specific welding applications. In this article, we will analyze various electrode types commonly used in nut projection welding, their features, and their suitability for different scenarios.
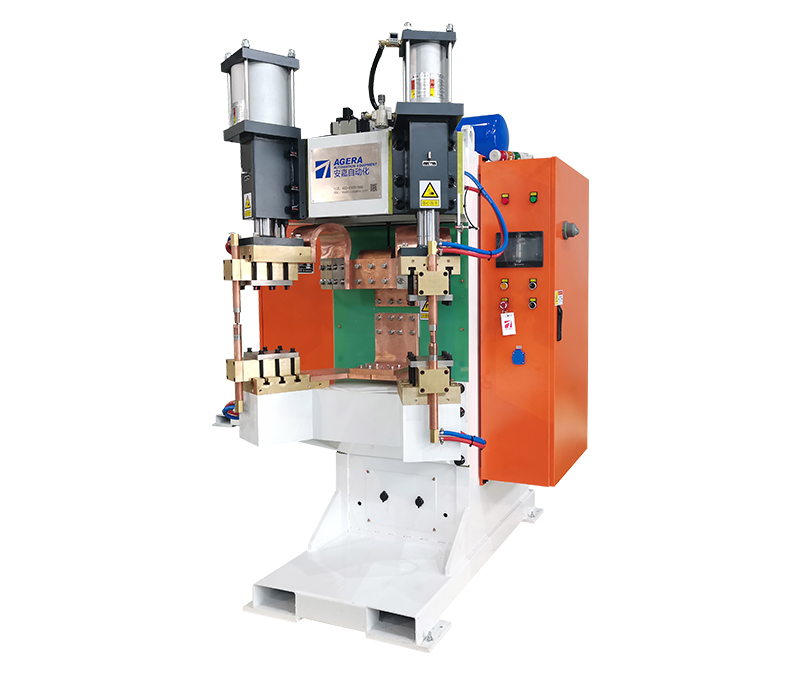
- Flat Electrodes: Flat electrodes are the most commonly used type in nut projection welding. They have a flat contact surface that provides uniform pressure distribution during welding. Flat electrodes are versatile and suitable for a wide range of nut sizes and materials. They offer good stability and can deliver consistent weld quality.
- Tapered Electrodes: Tapered electrodes have a conical shape, with a smaller diameter at the tip. This design allows for concentrated pressure at the weld joint, resulting in improved fusion and reduced spatter. Tapered electrodes are often used for welding smaller nuts or in applications where precise control of heat input is required.
- Dome Electrodes: Dome electrodes have a convex-shaped contact surface that provides increased pressure at the center of the weld joint. This design helps in achieving deeper penetration and better weld fusion. Dome electrodes are suitable for welding thicker materials or in cases where a stronger weld joint is desired.
- Ring Electrodes: Ring electrodes consist of a circular shape with a central hole. They are used for welding nuts with a recessed or protruding feature, allowing for precise alignment and contact. Ring electrodes provide uniform pressure distribution and are effective in achieving consistent welds on nuts with varying geometries.
- Multi-Spot Electrodes: Multi-spot electrodes are designed to simultaneously weld multiple nuts in a single operation. They feature multiple contact points, enabling efficient and high-speed welding. Multi-spot electrodes are commonly used in mass production environments where productivity and cycle time reduction are critical.
The selection of the appropriate electrode type plays a significant role in the success of nut projection welding. Flat electrodes offer versatility and stability, while tapered electrodes provide concentrated pressure and reduced spatter. Dome electrodes offer deeper penetration, and ring electrodes are suitable for nuts with specific features. Multi-spot electrodes enable high-speed production. By understanding the characteristics and suitability of each electrode type, manufacturers can make informed decisions and optimize their nut projection welding processes.