Resistance spot welding is a widely used method in various industries for joining metals. The effectiveness and quality of this process largely depend on the materials used for the welding electrodes. In this article, we will explore the key factors to consider when selecting electrode materials for resistance spot welding machines.
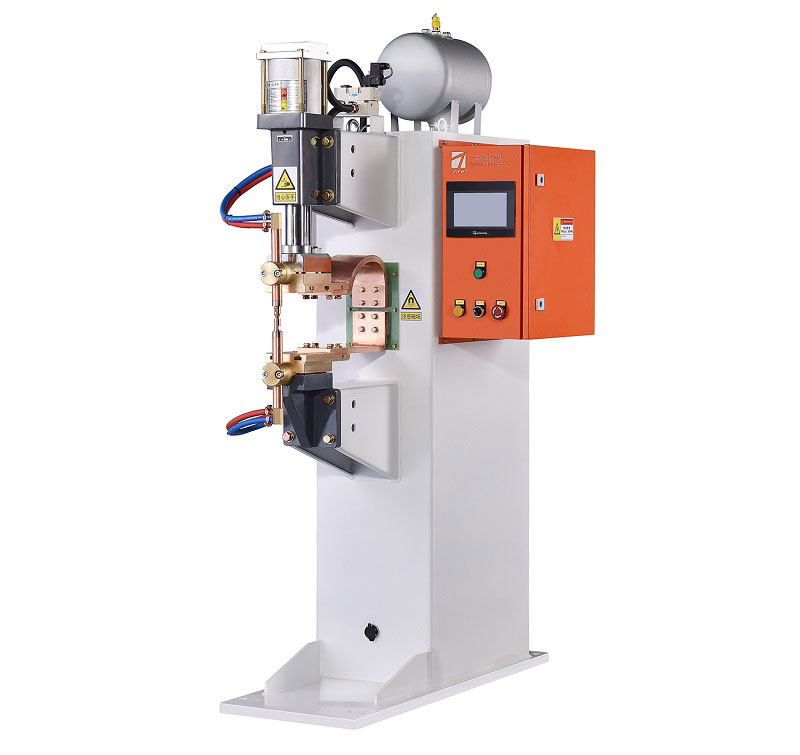
- Conductivity: The electrical conductivity of the electrode material is crucial for efficient heat generation during spot welding. Copper and its alloys, such as copper-chromium and copper-zirconium, are popular choices due to their high electrical conductivity. They allow for better energy transfer and help in achieving consistent welds.
- Heat Resistance: Resistance spot welding generates a significant amount of heat, especially at the contact points of the electrodes. Therefore, the chosen electrode material must possess excellent heat resistance to withstand prolonged operation without deformation or degradation. Refractory metals like tungsten and molybdenum are known for their exceptional heat resistance.
- Hardness: To ensure a stable and consistent weld, the electrode material should have sufficient hardness to resist wear and deformation during welding. Harder materials can maintain their shape and provide a reliable welding surface for an extended period. Materials like copper-chromium-zirconium (CuCrZr) are known for their high hardness and durability.
- Thermal Conductivity: Apart from electrical conductivity, thermal conductivity is also an important factor. Efficient heat dissipation from the weld area is essential to prevent overheating and maintain weld quality. Copper-based electrodes, due to their high thermal conductivity, are often preferred for this reason.
- Welding Process and Material Compatibility: Consider the specific welding process and the materials being joined. Different applications may require different electrode materials. For example, when welding high-strength steels, electrodes with good resistance to wear and deformation under high pressure may be necessary.
- Cost Considerations: The cost of electrode materials can vary significantly. While materials like pure copper offer excellent conductivity, they may not be cost-effective for all applications. Balancing performance requirements with budget constraints is essential.
- Maintenance: Regular electrode maintenance is crucial for the longevity of the welding equipment. Some electrode materials may require more frequent maintenance than others. Consider ease of maintenance when selecting electrode materials.
In conclusion, the choice of electrode materials plays a critical role in the performance and efficiency of resistance spot welding machines. Engineers and manufacturers must carefully evaluate the specific requirements of their welding applications and select materials that offer the right balance of conductivity, heat resistance, hardness, and cost-effectiveness. Proper maintenance practices should also be implemented to ensure the electrodes’ longevity and consistent weld quality.