Projection welding is a commonly used technique in nut spot welding machines that offers several advantages over other welding methods. In this article, we will explore the benefits and advantages of using projection welding in nut spot welding applications. Understanding these advantages can help manufacturers make informed decisions when choosing the appropriate welding method for their specific needs.
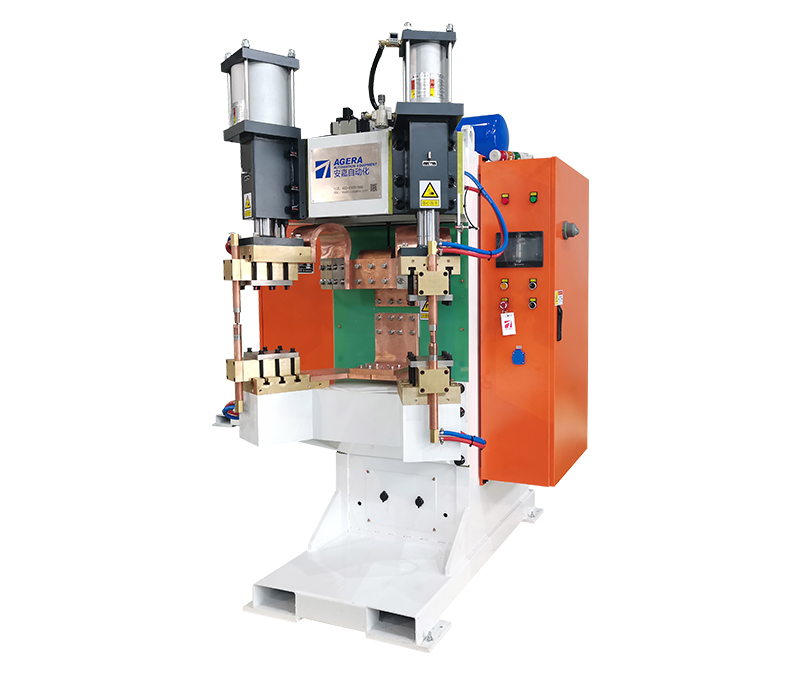
- Enhanced Joint Strength: Projection welding creates strong and durable welds by concentrating the heat and pressure at specific projection points on the workpiece. This results in a robust joint that can withstand high loads and vibrations, ensuring the structural integrity of the assembled components.
- Increased Productivity: Projection welding offers high-speed and efficient welding, leading to improved productivity in manufacturing processes. The process is fast, with welding cycles typically completed in milliseconds, allowing for rapid production and shorter cycle times compared to other welding methods.
- Reliable and Consistent Results: Projection welding provides consistent and repeatable results, ensuring uniform weld quality across a large number of welds. The controlled heat input and precise pressure applied at the projection points contribute to consistent fusion and excellent weld integrity.
- Minimal Surface Preparation: Unlike some other welding methods, projection welding requires minimal surface preparation of the workpieces. The projections on the nut or workpiece concentrate the heat and pressure, facilitating weld formation without the need for extensive surface cleaning or removal of coatings.
- Versatile Application: Projection welding is versatile and can be applied to various materials, including mild steel, stainless steel, and aluminum alloys. It is commonly used in automotive, aerospace, electrical, and appliance industries for joining nuts, studs, and other fasteners to sheet metal or other components.
- Cost-Effective Solution: Projection welding offers cost savings due to its high efficiency and minimal material preparation requirements. The fast welding cycles and reliable results minimize the need for rework or repair, reducing production costs and increasing overall profitability.
- Reduced Heat Affected Zone: Projection welding produces a localized heat-affected zone (HAZ), limiting the heat transfer to the surrounding areas of the workpiece. This helps to minimize distortion, warping, and material degradation, particularly important when working with thin or heat-sensitive materials.
- Automation and Integration: Projection welding can be easily integrated into automated production lines, allowing for seamless integration with robotic systems and increased production capacity. Automated nut feeding, electrode positioning, and control systems further enhance productivity and process control.
Projection welding offers numerous advantages in nut spot welding applications. Its ability to create strong joints, increase productivity, provide consistent results, and accommodate a wide range of materials make it a preferred choice in various industries. Additionally, the cost-effectiveness, minimal surface preparation requirements, and suitability for automation contribute to its popularity. Manufacturers can leverage these advantages to optimize their production processes, enhance product quality, and achieve efficient and reliable welds in nut spot welding applications.