Energy storage spot welding machines are versatile tools used for welding various workpieces with different specifications. To ensure optimal weld quality and integrity, it is essential to adjust the welding specifications according to the specific requirements of each workpiece. This article provides insights into the process of adjusting welding specifications in energy storage spot welding machines for different workpieces, enabling operators to achieve precise and reliable welds.
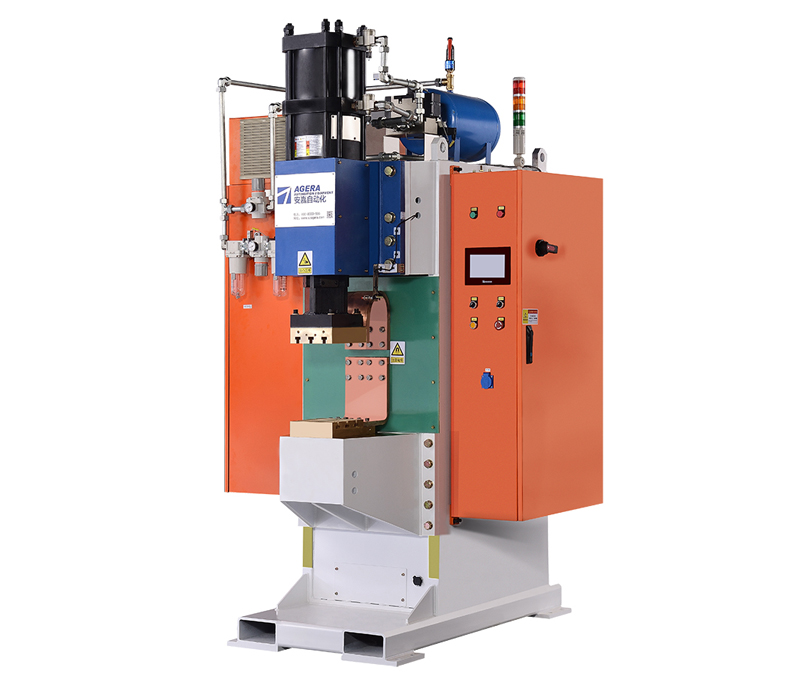
- Determine Welding Parameters: The first step in adjusting welding specifications is to determine the appropriate welding parameters for the specific workpiece. Factors such as material type, thickness, geometry, and desired joint strength influence the selection of welding parameters. These parameters typically include welding current, welding time, electrode force, and electrode shape. Refer to welding standards, material specifications, or guidelines provided by the workpiece manufacturer to establish initial welding parameter settings.
- Conduct Test Welds: Once the initial welding parameters are set, it is crucial to conduct test welds on sample workpieces. This allows for the evaluation of weld quality and the fine-tuning of the welding specifications. Examine the weld bead size, penetration depth, and visual appearance of the weld to assess its quality. Additionally, perform mechanical tests such as tensile or shear tests to determine the strength and integrity of the weld. Adjust the welding parameters as necessary to achieve the desired weld characteristics and meet the required standards.
- Consider Workpiece Variations: Different workpieces may have variations in material properties, thicknesses, or joint configurations. It is important to consider these variations when adjusting welding specifications. For instance, thicker workpieces may require higher welding currents or longer welding times to ensure sufficient heat penetration. Similarly, different materials may have varying heat conductivity, requiring adjustments in welding parameters to achieve optimal heat distribution and fusion.
- Optimize Electrode Selection: The choice of electrodes can significantly impact the welding process and weld quality. Select electrodes that are suitable for the specific workpiece material and joint configuration. Consider factors such as electrode material, shape, size, and coating. Different electrode combinations may be necessary for dissimilar materials or specialized joints. Regularly inspect and maintain the electrodes to ensure proper alignment, sharpness, and cleanliness, as worn or contaminated electrodes can adversely affect weld quality.
- Document Welding Specifications: To ensure consistency and repeatability, it is essential to document the adjusted welding specifications for each workpiece. Maintain a comprehensive record of the welding parameters, electrode selection, and any additional considerations specific to each workpiece type. This documentation serves as a valuable reference for future welding operations and facilitates efficient setup and troubleshooting.
Adjusting welding specifications for different workpieces in energy storage spot welding machines is crucial to achieve reliable and high-quality welds. By determining appropriate welding parameters, conducting test welds, considering workpiece variations, optimizing electrode selection, and documenting the specifications, operators can effectively adapt the welding process to meet the specific requirements of each workpiece. This approach ensures consistent and successful welding outcomes, resulting in strong and durable joints.